Forum Discussion
JBarca
Oct 14, 2013Nomad II
mrekim wrote:JBarca wrote:
If you still need help with this and you have a 1/2" torque wrench that will go say 200 ft lb or even 150, I can offer some help.
I have a 150 ft/lb beam torque wrench.JBarca wrote:
I do happen to have a 700 ft lb torque wrench. And there are other proven methods of obtaining the correct torque. If you can get it to a known 150 or 200, you can scribe a line in the nut and head and I can get you the nut rotation required past that torque to get 450.
We just need to know if we are talking lubed threads ( and what kind of lube) or dry threads.
Dry (fine, I think) threads. 1.25.
Hi mrekim,
Sorry this took so long. I took pics etc last weekend but then had to go out of town for work. Here is a method that may help the cause.
I repeated this torque to position method 3 times and it repeats within an acceptable tolerance. I'll do this in pics for easier understanding.
For the 1 1/4" ball nut needing 450 ft. lb. of torque.
Start with dry threads. (These values will not work on lubed threads)
Pre-torque to 100 ft. lb. I picked 100 as most RV'ers should have a torque wrench for lugs nuts on the camper and most 1/2" torque wrenches go higher than this anyway.
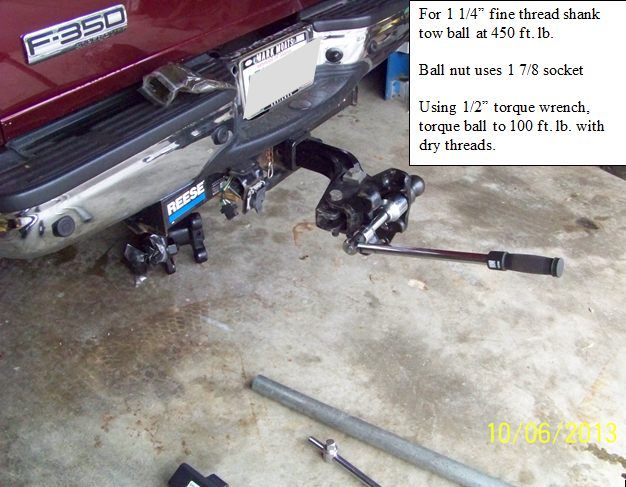
After pre-torquing we need to mark the ball shank, hitch head and the ball nut. We need to know if the ball slips any during the heavier torquing process. I used a black sharpie marking and a straight edge to draw a line across all 3. The red lines are so you can see it in the pics.
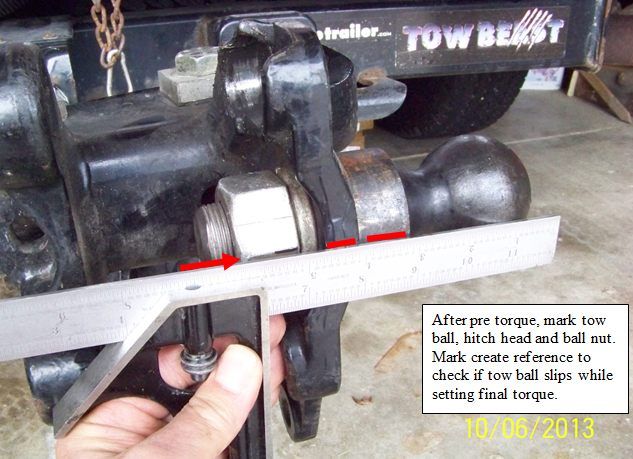
Using a 3/4 breaker bar or other tool, torque to the following position. For this test, I used my 3/4" torque wrench to establish the position on 450 ft. lb. so we can see the rotation.
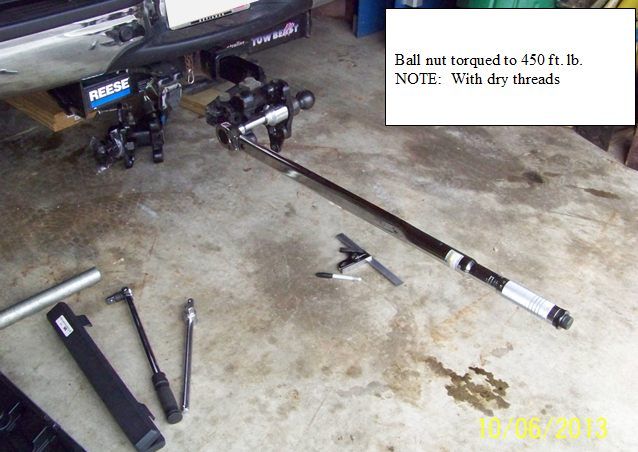
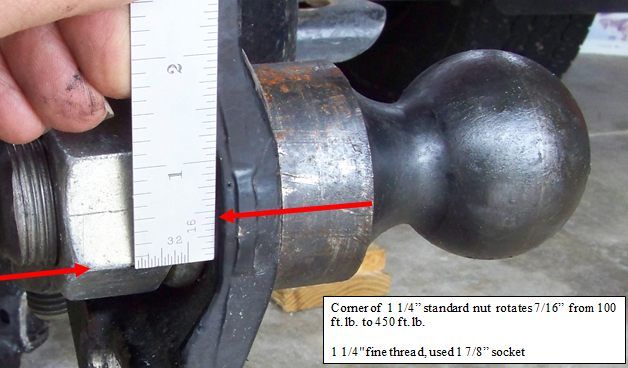
You can see the nut corner moved 7/16" to get to 450 ft lb. This repeated twice and the 3rd time it was 1/2". So between 7/16" and 1/2" will do it. Note: This was on "dry" threads.
While I was at it, I did the hitch head bolts too.
For the 3/4" grade 8 hitch head bolts needing 300 ft lb of torque.
Start with dry threads. (These values will not work on lubed threads)
Pre-torque to 100 ft. lb.

Mark the bolt head to the serrated washer and the nut to the serrated washer. We need to know if the bolt slips any during the heavier torquing process. I used a black sharpie marker.
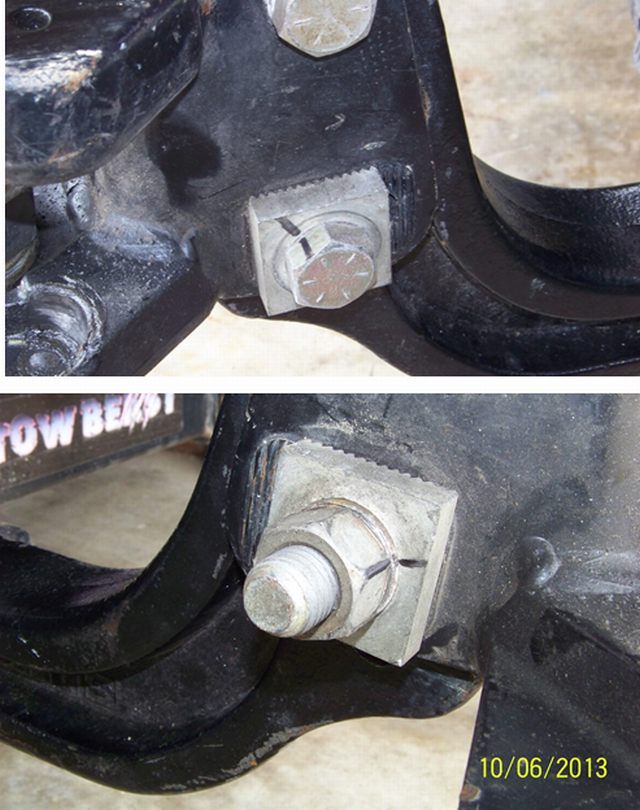
Using a 3/4 breaker bar or other tool, torque to the following position. I used my 3/4" torque wrench to establish the position on 300 ft. lb. so we can see the rotation.
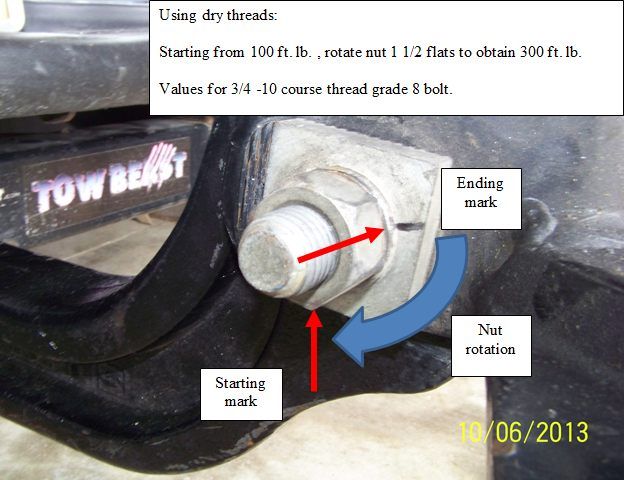
In this case the nut moved 1 1/2 flats. This diameter bolt needed more rotation from where I was measuring, so counting flats seemed to fit better to reproduce. Two of the 3 tests came out on 1 1/2 flats, the 3rd came out 1 5/8 flats. If you are between this tolerance you should be good.
This method of "torque to position" from a know pre-torque offers a better known outcome over the weight of a person hanging on a length of pipe. The weight x distance in pure theory should work, however it came up short for me as compared to the torque wrench. Possibly likely due to inefficiency of a cantilevered wrench.
Also to note, there is some small error in these tests. This method is only as good as the calibration and repeatability of my torque wrench. However comparing this method to using nothing, an impact wrench, or the body weight x distance method your chances of getting adequate torque to a spec. are better.
Hope this helps
John
About RV Tips & Tricks
Looking for advice before your next adventure? Look no further.25,129 PostsLatest Activity: Apr 26, 2025