There is more to it than just air pressure, though important, it is just part of the whole system
Designed a tire stand for either or both DOT & RMA back while in college. Also working as a tire monkey to both pay for college and support my track/rally/etc days.
Part-time working at a small industrial controls company and one of the full time engineers was having problems with a contract and the owner/boss knew my love of automotive, so he assigned me to help. That turned out to become my project.
Specification was to replace an old hydraulic tire stand they had been using for decades and our controls the best at that time (solid state controllers & power converters). Precision was our big sell.
The old guy already did the calculations and ordered a refurbished GE locomotive traction motor and I had already designed the stand (1" & 1/2" plate with many vertical sections made up of square & C-channel...with tons of gussets).
The drum that tires were in contact with was about 5 foot in dia and had a textured surface. That was directly driven by the traction motor.
The tire/wheel was mounted on a 5 axis arm and each axis had its own electric motor. The tire/wheel could either drive the drum (5th axis), or freewheel on the drum.
They sent us about 5 tire/wheel combos for our testing to their specification. "Weight" (how hard #1 axis would push onto the drum), "Slip angle" (#2, off center of rotation), Accel/Deccel, Speed (#4 and hardest was rate of change they spec'd out) and can't remember the others
Two acceptance tests by 'them' and they showed up with a trailer full of tires & a tire machine to change them.
Their testing stunk up the whole shop/welding/testing/stockroom with burnt rubber smell. So the boss told them to do at night.
Since only part-time, still in college and trying to be a boy-racer on a very limited budget...LOVED that they were working after everyone was gone.
Made friends with them, and they even put my wheels on our machine (they hadn't accepted it yet). Learned tons and loved their new to me, IR heat gun (big compared to the ones we have today)
Another engineer and I even made them a custom adjustable strobe to freeze the image. Cool being able to see the tire sidewall's wave and ripples during high stress at 100 MPH.
Back on topic...
Rim width vs tire section width vs aspect ratio plays huge on how a tire behaves.
Pressure affects the amount of sidewall 'bend' and the rim affects the amount of tire 'bend-back'. Aspect ratio plays with them all.
Searched for what wanted to discuss and here are some images & comments

This shows the relationship between rim width and tire's flex points (part of the sidewall bend-back)
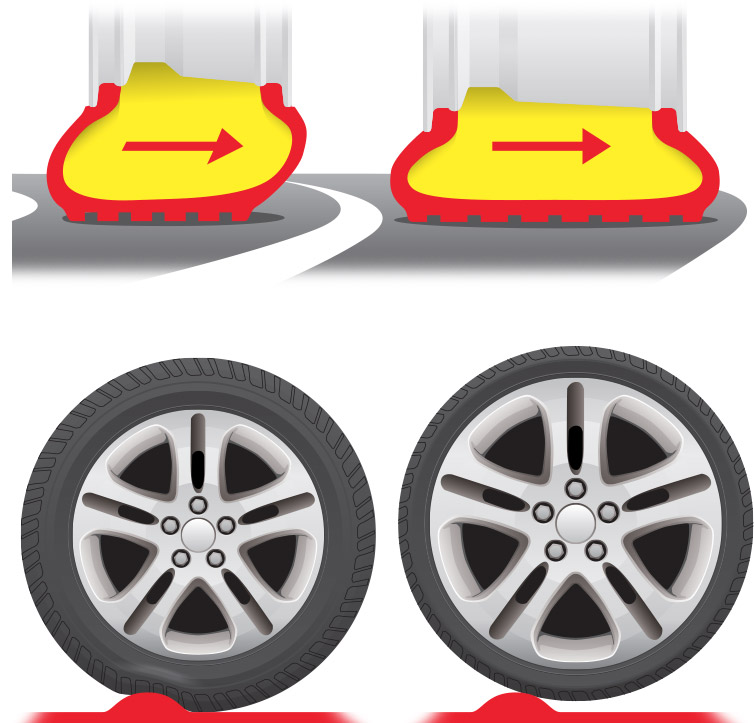
This is another image showing rim with and aspect ratio. How the tires 'bend-back' 'rolls over' during cornering or sweeping curves. When that tire straightens back, the wheel to tire will 'wallow' back and forth until normal.
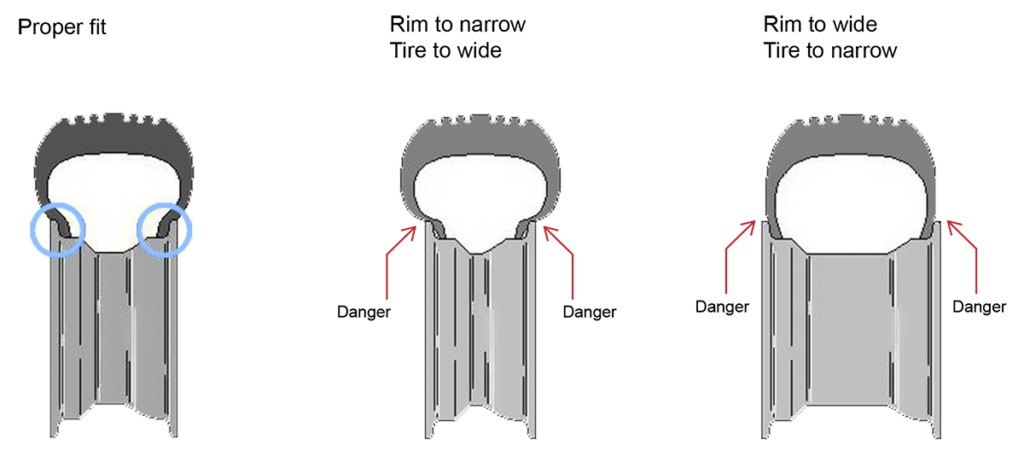
This image shows how a tire bead fits on various rim widths. From too narrow, just right, to too wide.
All tire specifications will list a range of rim widths for 'that' tire. Too narrow well have more sidewall bend-back and provide the best or highest level of ride quality. Wider will have little sidewall bend-back and will be the poorest in ride quality. Plus, narrower rims cost the OEMs less than wider rims.
So, it depends on more than just PSi, but the rim width vs tire section width vs aspect ratio.
The more sidewall bend-back, the softer the ride (higher ride quality), but it will have a larger slip angle and has to move the wheel back and forth from side to side during corner or sweeping curves.
Less sidewall bend-back will have the smallest slip angle and responsiveness greatly increased, but harsher ride
Why I like wider rims. My 1996 K3500, 7.4L Suburban has LT265/75R16E tires on 10x16 alloys and LOVE it that way. Most think it rides like a truck...which it is and the way I like it.
It also is super responsive to steering input. Steering input happens *NOW*.