Jfet wrote:
hi westend,
I got some of the 2 inch R-Max TSX-8500 exposure rated polyisocyanurate foam (expensive!) now. Do you think I need to aluminum tape the sides of the foam when I cut them to fit inbetween my wall studs? The foam would otherwise be exposed on the 2 inches of thickness, but would be pressed up against my steel studs.
No, I wouldn't seal the cut foam. I'm guessing the thoughts about sealing the foam are generated from consideration about moisture absorption? I wouldn't worry about it. You can do some experimentation with absorption by soaking a small piece of foam under water. Weight down the foam piece under water and let it soak for a few days (weeks, months?). Remove the weight and see if you have the same amount of flotation. A trip to the beach will also show that most extruded/expanded foam is difficult to saturate.
One advantage to metal studs is that it bespeaks the walls being set up on a jig in the factory, resulting in cavities that are plumb and square. I did not have one cavity that was plumb, some differing in dimension by as much as 1/2", latitudinally, in my wood-studded trailer. Every piece of foam needed to be measured and custom cut. If you have metal studs, I would strongly suggest you investigate the use of an additional thermal break between the studs and the interior paneling. It may be that the climate in your area doesn't warrant it but conductive heat transfer from the outer siding through the studs can be significant. At one point, I added up the surface area of the stud and ceiling joist faces and came up with a figure of around 40 sq. ft., IIRC. That is equivalent to having a 4'x8' sheet of paneling that is close to ambient temp inside the trailer. As mentioned, I installed a thermal break of 1/4" fanfold insulation across the walls. The fanfold insulation is cheap and is easy to install on wood studs, staples were used. With metal studs, it would need to be glued with foam adhesive.
Fanfold being installed:
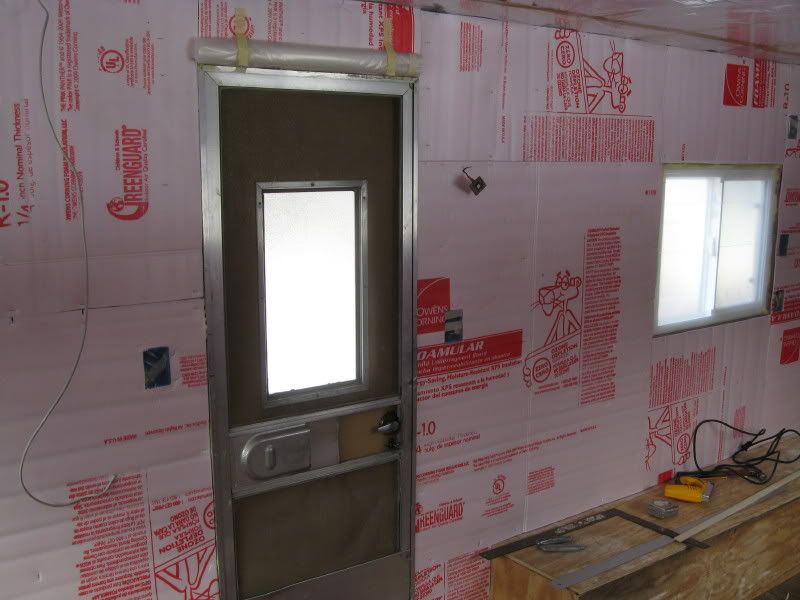