JBarca
Feb 04, 2017Nomad II
Bent Main Frame Rail Below Slide - (Picture Heavy)
Hello Fellow Campers,
I’m inquiring if you or someone you know has run into where the main frame rail (thin I beam style) bent down behind the rear spring hanger and if you know any of the details surrounding it? This is a somewhat technical & long post by it's nature and I will try to keep it short as I can and use pictures get the point across. I have searched the web for this type of failure and to date have not found this type of issue. I have found a lot of bent A Frames, spring hangers and I beam web cracks. Mine is different. I did find one where the frame did failed in a similar manner and it was here on RV.net. See here. Bent Frame and breaks However in this case, the camper was in an accident where the camper become air born, dropped down hard on the road and bent the frame rail in one very large event.
Background: This past fall on our last campout, our slide room would no longer retract without heavily binding on the top rear and lower front sides of the slide. This issue has been ongoing for several years and has progressed worse over time. Basically, the slide opening in the camper wall is out of square in relation to the square slide room. In the past I could fudge the slide adjustment to get the system to work. I am now out of the adjustment.
After measuring the camper, I found the main frame rail below the slide is bent down just aft of the rear axle spring hanger. By pulling a string along the bottom of the frame, starting at the front spring hanger all the way to the rear camper wall, the area between the spring hangers is straight. There is a bend down aft of the rear hanger and then the frame is straight all the way to the back wall. If I jack up the slide side frame rail at the end of the frame 3”, the bottom of the frame is now straight and the slide opening is back to true square.
We bought the camper in Oct, 2007 and I have pictures documenting several upgrades over the years to the running gear. Added new axles to correct axle alignment, added; shocks, rubber equalizer, hanger stiffeners, self-adjusting brakes and 15 to 16” LT tire upgrade. Through these pictures I can see when the frame lower flange was straight and when deformation started.
During the summer of 2010, we were towing across NY state on I-88 heading west out of the Amsterdam area into Corning NY. The state had started resurfacing from the eastern end heading west, however the last 15 miles was still old road. That last 15 miles was old concrete road and brutal with pot holes. We were somewhat trapped having to stay with in the right lane with no exits until we got off. Passing semis/cars etc. in the left lane and It was pot hole after pot hole. I slowed to 45 to 50mph and dodged the pot holes I could and not create a speed hazard on the road. When we made it to camp, the inside of the camper was the worst shaken up ride we have ever had. At this time, I had no idea the frame may have been affected.
I have pictures months before our summer trip showing the frame was not yet deformed. By the end of 2010, the pictures were showing that lower flange deformation had started just I did not realize what it meant. After the event, we did a large quantity of normal towing which went on for the next 6 years but none with a pot hole cluster like I-88. The slide opening problem started around 2010 and become worse over time. At this point in my investigation, I feel the I-88 towing event started the lower flange deformation on the slide side frame rail and slowly over time continued to increase the frame rail bend downward making the slide opening out of square issue worse.
If you have seen this type of frame deformation before and have any details to it, please pass along. This is also a learning post that if you have the thin I beam type of frame, if you ever see any flange deformation, even slight damage, that is the sign of a problem. If I knew then what I know now, I could of corrected the issue much simpler back in 2010. I have a lot more information and can share if needed.
Here are pictures of the problem.
This first pictures are “before” the problem. Notice the gap between the slide flange and the camper flange. It is parallel like it should be. These pics are from the year we bought the camper.
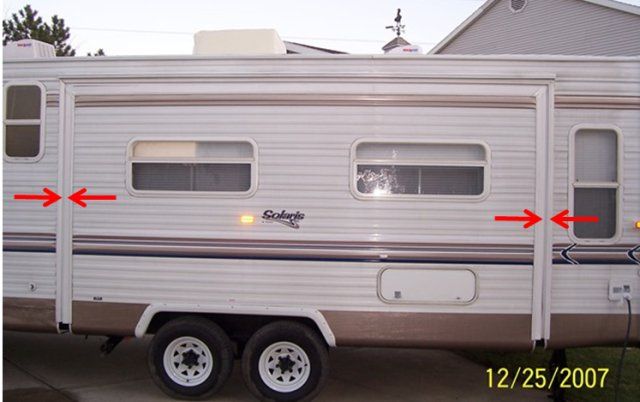
This is the lower flange behind the rear left frame hanger. Notice there is no distortion of the lower flange.
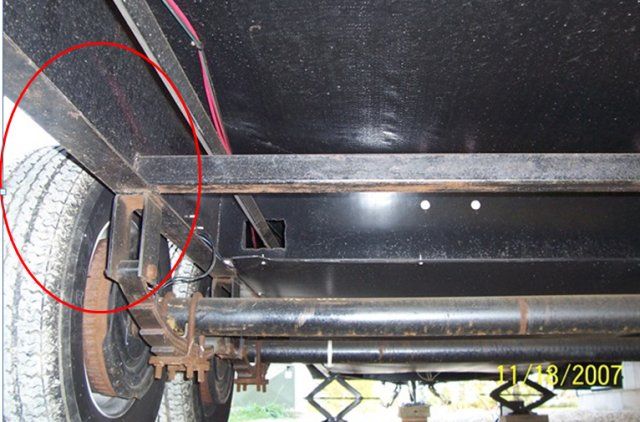
Now a few pics of time line leading up to current day. No damage yet in these pics.
2-8-2009 no damage
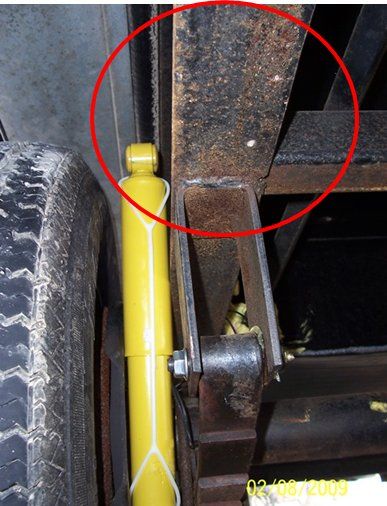
5-10-2009 adding reinforcement to prevent hanger flexing and lower flange bending and web cracking. No frame damage
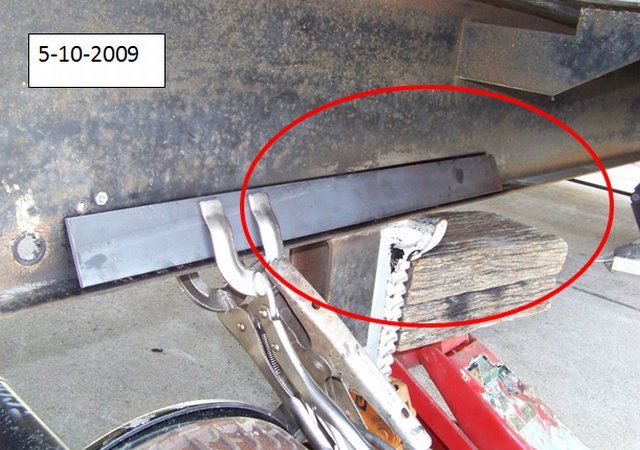
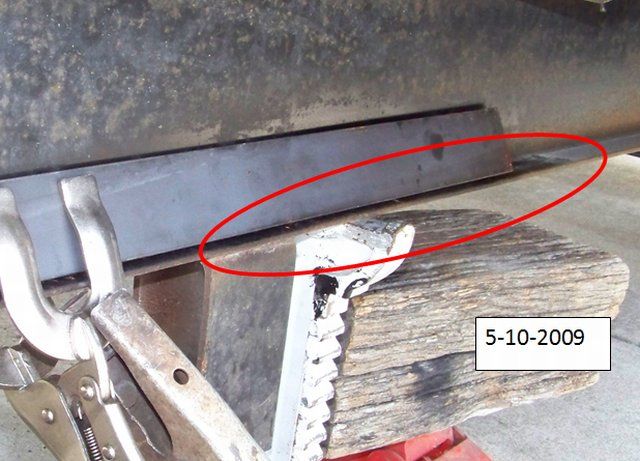
Now the start of damage. Picture taken on 12-11-2010 when adding rear shocks
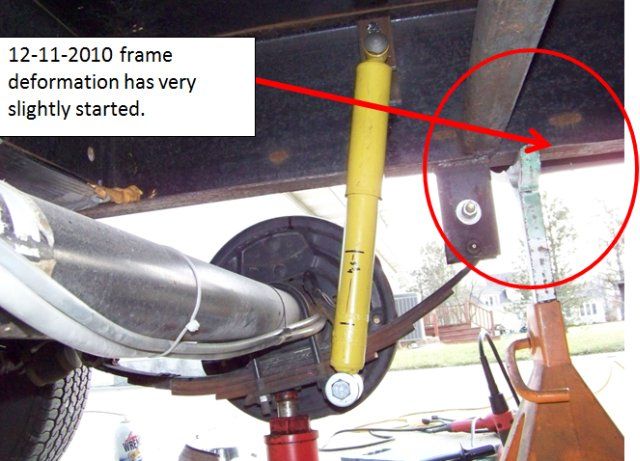
4-15-2012. Top rear of slide. Gap 3/4"
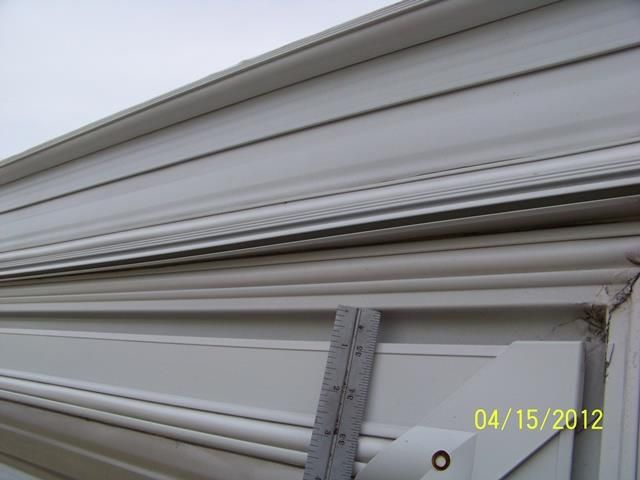
4-15-2012. Top front of slide. Gap 1 1/8" Must adjust slide arms to shift slide to fit camper hole better. This creates a situation inside were we do not lift off the carpet as much
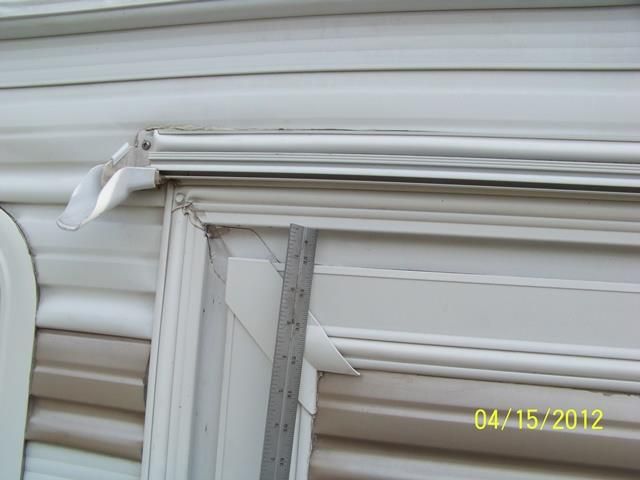
More on the next reply.
I’m inquiring if you or someone you know has run into where the main frame rail (thin I beam style) bent down behind the rear spring hanger and if you know any of the details surrounding it? This is a somewhat technical & long post by it's nature and I will try to keep it short as I can and use pictures get the point across. I have searched the web for this type of failure and to date have not found this type of issue. I have found a lot of bent A Frames, spring hangers and I beam web cracks. Mine is different. I did find one where the frame did failed in a similar manner and it was here on RV.net. See here. Bent Frame and breaks However in this case, the camper was in an accident where the camper become air born, dropped down hard on the road and bent the frame rail in one very large event.
Background: This past fall on our last campout, our slide room would no longer retract without heavily binding on the top rear and lower front sides of the slide. This issue has been ongoing for several years and has progressed worse over time. Basically, the slide opening in the camper wall is out of square in relation to the square slide room. In the past I could fudge the slide adjustment to get the system to work. I am now out of the adjustment.
After measuring the camper, I found the main frame rail below the slide is bent down just aft of the rear axle spring hanger. By pulling a string along the bottom of the frame, starting at the front spring hanger all the way to the rear camper wall, the area between the spring hangers is straight. There is a bend down aft of the rear hanger and then the frame is straight all the way to the back wall. If I jack up the slide side frame rail at the end of the frame 3”, the bottom of the frame is now straight and the slide opening is back to true square.
We bought the camper in Oct, 2007 and I have pictures documenting several upgrades over the years to the running gear. Added new axles to correct axle alignment, added; shocks, rubber equalizer, hanger stiffeners, self-adjusting brakes and 15 to 16” LT tire upgrade. Through these pictures I can see when the frame lower flange was straight and when deformation started.
During the summer of 2010, we were towing across NY state on I-88 heading west out of the Amsterdam area into Corning NY. The state had started resurfacing from the eastern end heading west, however the last 15 miles was still old road. That last 15 miles was old concrete road and brutal with pot holes. We were somewhat trapped having to stay with in the right lane with no exits until we got off. Passing semis/cars etc. in the left lane and It was pot hole after pot hole. I slowed to 45 to 50mph and dodged the pot holes I could and not create a speed hazard on the road. When we made it to camp, the inside of the camper was the worst shaken up ride we have ever had. At this time, I had no idea the frame may have been affected.
I have pictures months before our summer trip showing the frame was not yet deformed. By the end of 2010, the pictures were showing that lower flange deformation had started just I did not realize what it meant. After the event, we did a large quantity of normal towing which went on for the next 6 years but none with a pot hole cluster like I-88. The slide opening problem started around 2010 and become worse over time. At this point in my investigation, I feel the I-88 towing event started the lower flange deformation on the slide side frame rail and slowly over time continued to increase the frame rail bend downward making the slide opening out of square issue worse.
If you have seen this type of frame deformation before and have any details to it, please pass along. This is also a learning post that if you have the thin I beam type of frame, if you ever see any flange deformation, even slight damage, that is the sign of a problem. If I knew then what I know now, I could of corrected the issue much simpler back in 2010. I have a lot more information and can share if needed.
Here are pictures of the problem.
This first pictures are “before” the problem. Notice the gap between the slide flange and the camper flange. It is parallel like it should be. These pics are from the year we bought the camper.
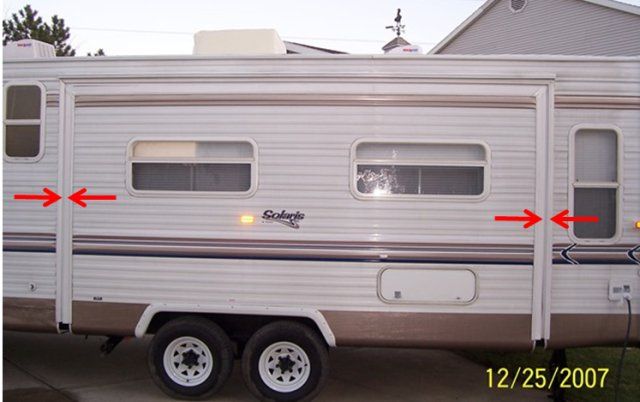
This is the lower flange behind the rear left frame hanger. Notice there is no distortion of the lower flange.
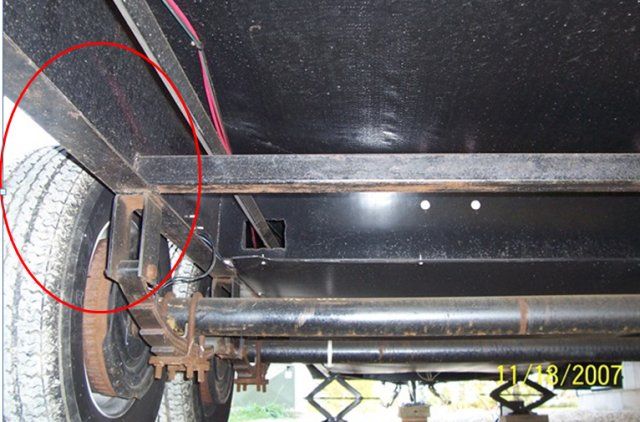
Now a few pics of time line leading up to current day. No damage yet in these pics.
2-8-2009 no damage
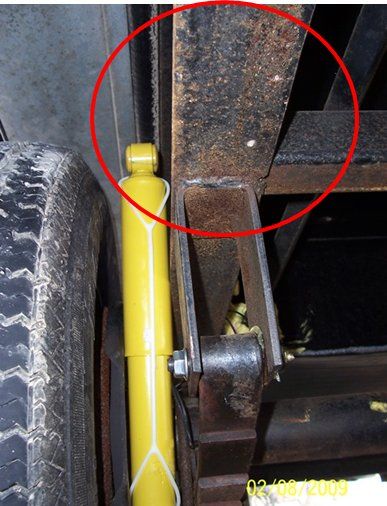
5-10-2009 adding reinforcement to prevent hanger flexing and lower flange bending and web cracking. No frame damage
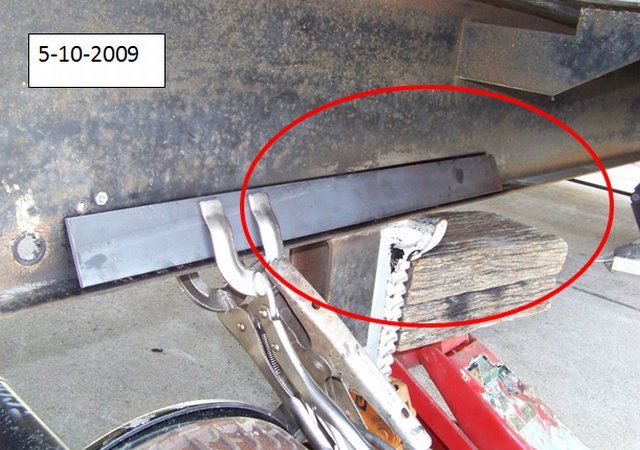
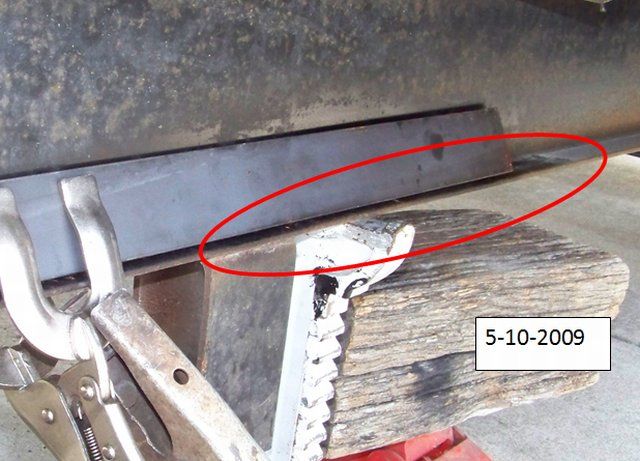
Now the start of damage. Picture taken on 12-11-2010 when adding rear shocks
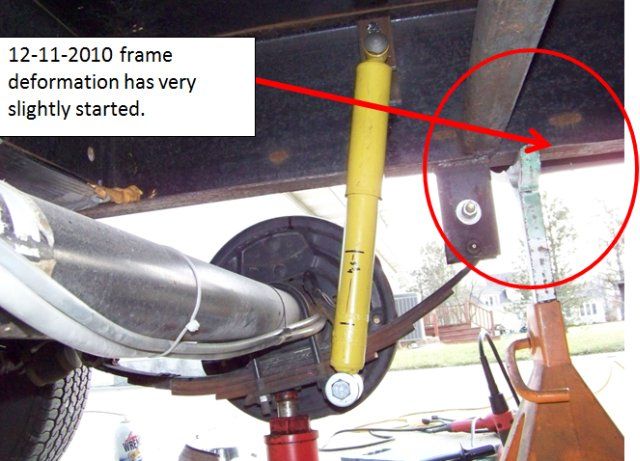
4-15-2012. Top rear of slide. Gap 3/4"
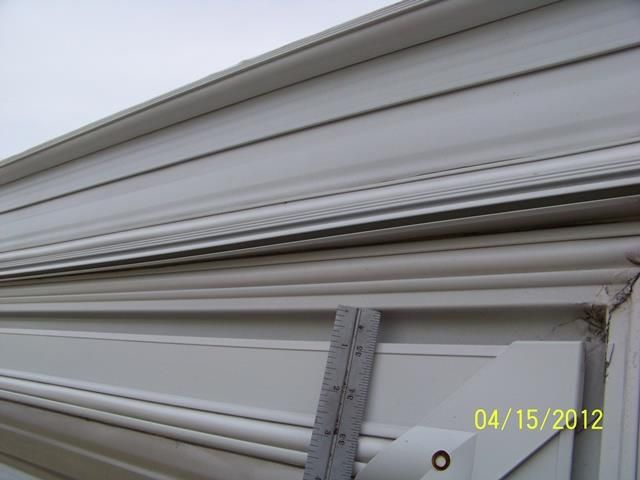
4-15-2012. Top front of slide. Gap 1 1/8" Must adjust slide arms to shift slide to fit camper hole better. This creates a situation inside were we do not lift off the carpet as much
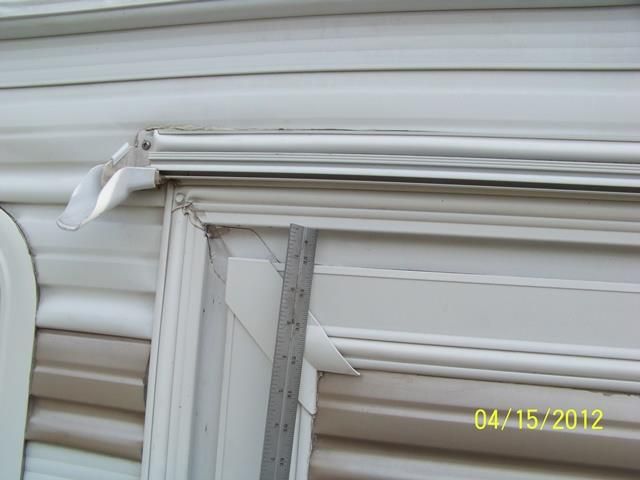
More on the next reply.