Forum Discussion
professor95
Jan 10, 2008Explorer
I wrote this back in Septmber 07 but never posted it to the forum. Perhaps the info herwithin will be of some benefit to members asking questions about sound abatement.
The sound or “noise” level of my first Chinese built 3,000 watt genset was acceptable at 67 dB. It met the maximum set by the National Park Service at a distance of 21 feet and was far and away quieter than any portable generator I had previously used with my travel trailer.
Still, it was loud compared to the available models sold as quite gensets like the Honda 3000I. A trip to the solitude of a National Forest campground confirmed that while the noise from the generator was within the set limits, it was too loud for the particular environment we were occupying.
I set out to come up with a way to reduce the sound level of the generator.
Experimentation almost immediately revealed that the noise was not from an inadequate muffler. In fact, the OEM muffler on the genset was more than adequate at reducing sound levels. Added resonators, extensions or diverting the exhaust through stacks and down pipes offered nothing.
Some rather crude testing using fiberglass insulation and heavy mover’s pads placed at various locations showed that the majority of noise was coming from the flywheel side of the engine and the area below the cylinder. The generator head (alternator) had a very low noise level. Just placing the insulation near or over the suspect areas could drop noise levels by 2-3 dB.
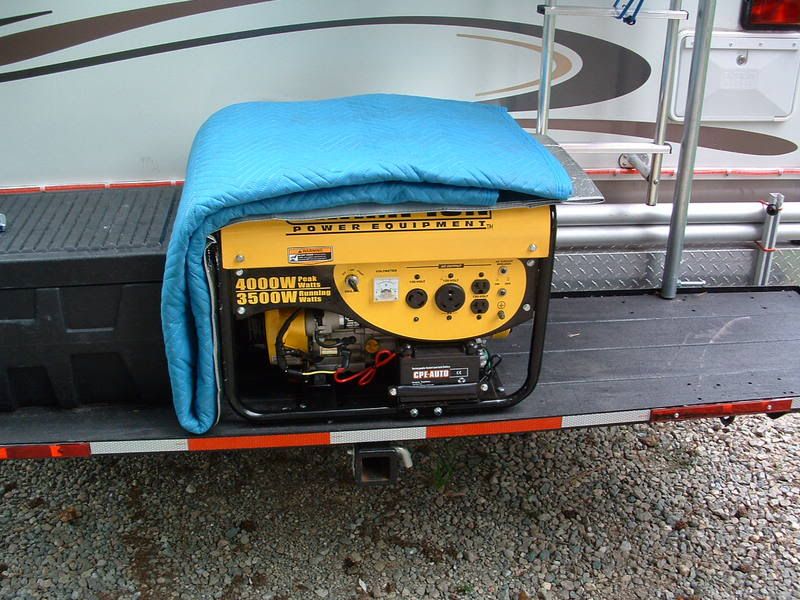
I then constructed a three sided enclosure with a top, keeping the alternator end open, out of ¼” fanfold polystyrene insulation board. It worked well in reducing sound levels to the 64 dB level on all but the open side. For a while I stored the thin insulation board under the mattress in the RV for use when the generator was needed. But, alas, it was a real hassle to drag it out and set it up. It also provided no real sound reduction benefit on the open end.
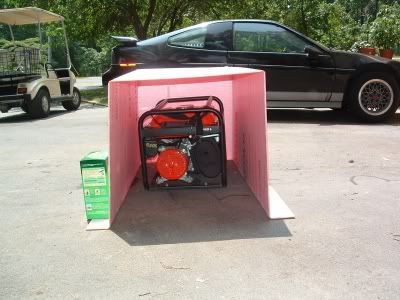
In September of ’06 I decided to make an enclosure for the entire generator. I settled on a rather elaborate design using numerous baffles to reduce sound paths and fans to assure adequate circulation of air for cooling the engine. I isolated the muffler with an ”L” shaped piece of aluminum and removed the gas tank. The major obstacles I encountered were providing power for the fans (the genset did not have a 12 volt DC output), designing a fuel delivery system for the now remote gas tank, radiant heat from the muffler raising internal temperatures – even with a heat shield – and the mass or bulk of the completed project. It was heavy, much larger than the original and in the long run way over built. Still, it did provide sound reduction on the order of 5 dB – a considerable amount when using the unit in an otherwise quite campground. I abandoned the enclosure later in the winter of ’07 believing I could come up with a better system.
In the Spring of ’07, before a trip back to the National Forest campground, I mounted the genset in the back of my truck (tow vehicle). I made some mounting skids from 2x4 lumber and constructed an exhaust pipe that exited through the roof of the truck’s fiberglass camper shell. This setup provided a significant reduction in sound but required opening a window on the camper shell and loosing some valuable storage space in the bed of the truck.

It proved to be only a temporary solution since I usually removed the camper shell during the summer so that the golf cart or jet ski could be placed in the truck bed and carried with us on our trips to the beach or lake.
By the summer of ’07, I had acquired two new Chinese built gensets. One was an electric start Champion 40008 capable of producing up to 4,000 watts of power at 120 volts, the other was a 7,500 peak watt unit utilizing an engine similar to the 13 HP Honda GX390. While the output of the smaller genset destined for RV use had been improved, the sound level had not. I had also become interested in using propane as an alternate fuel for gensets and successful converted both a Generac 5,500 and my new Champion 7,500 watt home back-up power generator to run on propane from an underground 300 gallon tank. Propane was the perfect fuel for my home generator; it did not go bad when stored for long periods of time and it was easy for me to store large quantities.
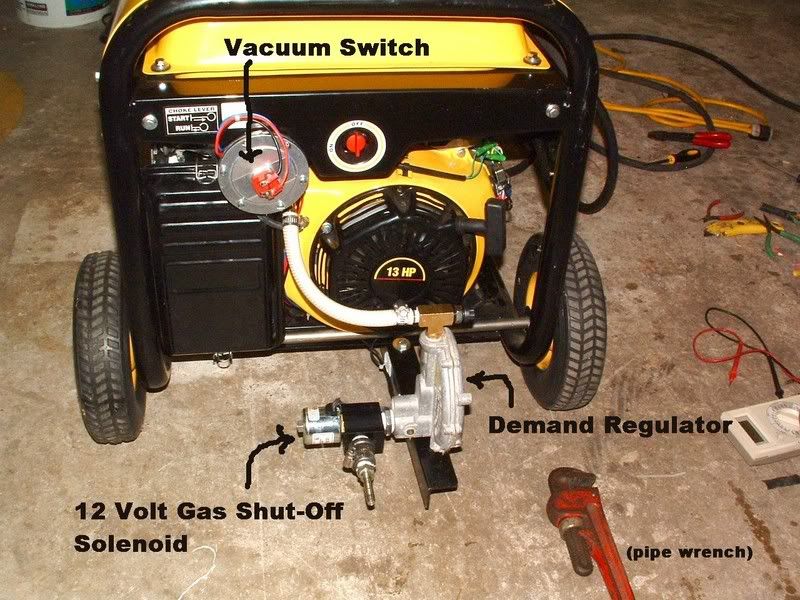
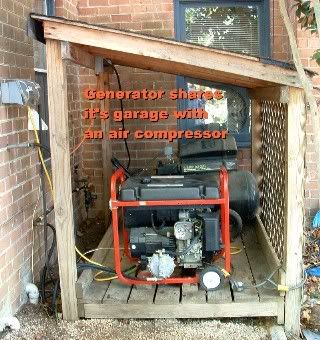
Both factors were extreme priorities after spending two weeks without commercial power after hurricane Isabel and one week after tropical storm Gaston. I required about 100 gallons of gasoline to keep the backup generator running during the aftermath of Isabel - no small feat in itself.
By late summer of ’07 my attention once again turned to some type of sound abatement enclosure for the Chinese built generator I used with the RV.
My previous attempts at building a sound abatement enclosure had taught me what NOT to do. I now knew that there were two priorities that would have to be met to insure some form of success:
1. The muffler had to be outside of the enclosure to lower internal temperatures. Efforts to shield the muffler inside the enclosure had been disappointing.
2. The fuel tank (or fuel source) could not be inside the enclosure. From a safety perspective, I was not comfortable with gasoline being inside a closed compartment.
I began to conduct some much needed research on the characteristics of sound waves along with their propagation and reproduction. Not surprisingly, the best source of information was found from elements of acoustical design. Buildings, auditoriums, speaker cabinets and even boom cars all draw from the same basic principles.
In designing a new enclosure, there were four basic principles that had to be considered; reflection, absorption, frequency and amplitude.
Through measurements made with a microphone, graphic equalizer and oscilloscope it was determined that the majority of sound energy was, as expected, under 5,000 Hz.
The amplitude had previously been established through measurements with a digital sound level meter and manufacturer’s data.
Since the sound frequencies were below 5,000 Hz, a small enclosure would do a better job of canceling the sound waves. Low frequencies have a longer wave length or period than high frequencies - the smaller the cabinet, the more attenuation of low frequency sound will occur. Audiophiles depend upon large diameter speakers, cabinets and tuned reflex ports for low frequency reproduction. Conversely, small diameter speakers and cabinets do a better job of reproducing high frequencies.
Anyone who has ever hooked up a set of speakers knows that they must be equally phased to reproduce sound properly. If one speaker is out of phase, or pulling the speaker cone in while the opposite speaker is pushing the cone out, the resultant sound waves will somewhat counter each other. Reflection of sound waves would be important in an enclosure to reduce sound pressure.
Absorption of sound waves turned out to be a considerably more complex than I originally believed. While it is true that materials with an open cellular structure can do an effective job of absorbing sound, caution must be exercised in selecting the material to assure there is sufficient density to cancel the effects of sound transmissions. Simply stated, when sound waves hit the surface of some materials the molecules in the material can also move or vibrate at the same rate as the sound pressure pushing against the material. Density, or thickness, of the material is a factor for consideration.
Add to all this my personal requirement that whatever I built to house the genset must not, in any way, compromise the original construction so that I could not at a later date return the genset to its original condition.
For my particular application, maintaining portability of the genset was not a priority. I had previously built a carrier on the back of my TT (with proper consideration for weights) and intended to permanently mount the genset square in the middle of the carrier. This would allow external mounting of the muffler under the carrier.
OK, let’s review both my personal requirements and needed elements to make the project successful:
1. Make no changes to the original genset that cannot be reversed.
2. Allow for adequate airflow to cool the engine and alternator, keeping the absolute maximum temperature under 175 degrees F.
3. Create a remote fuel source.
4. Move the muffler out of the enclosure.
5. Make the enclosure small.
6. Build the enclosure from materials that allow both reflection and absorption of sound waves.
Based on my findings, the ideal enclosure would be a perfect hemisphere (ball), the walls would be about 6” thick and made of both low density and high density material and there would be multiple small openings of less than 2” that could be tuned by inserting or withdrawing tubes (tuned port theory). Not a very practical item to build or use. A compromise enclosure containing all of the possible elements would have to be designed and built.
I did design and built such an enclosure and shared the construction/results on the forum.

Sound presssure at 21 feet was....

Professor Randy T. Agee
September 2007
The sound or “noise” level of my first Chinese built 3,000 watt genset was acceptable at 67 dB. It met the maximum set by the National Park Service at a distance of 21 feet and was far and away quieter than any portable generator I had previously used with my travel trailer.
Still, it was loud compared to the available models sold as quite gensets like the Honda 3000I. A trip to the solitude of a National Forest campground confirmed that while the noise from the generator was within the set limits, it was too loud for the particular environment we were occupying.
I set out to come up with a way to reduce the sound level of the generator.
Experimentation almost immediately revealed that the noise was not from an inadequate muffler. In fact, the OEM muffler on the genset was more than adequate at reducing sound levels. Added resonators, extensions or diverting the exhaust through stacks and down pipes offered nothing.
Some rather crude testing using fiberglass insulation and heavy mover’s pads placed at various locations showed that the majority of noise was coming from the flywheel side of the engine and the area below the cylinder. The generator head (alternator) had a very low noise level. Just placing the insulation near or over the suspect areas could drop noise levels by 2-3 dB.
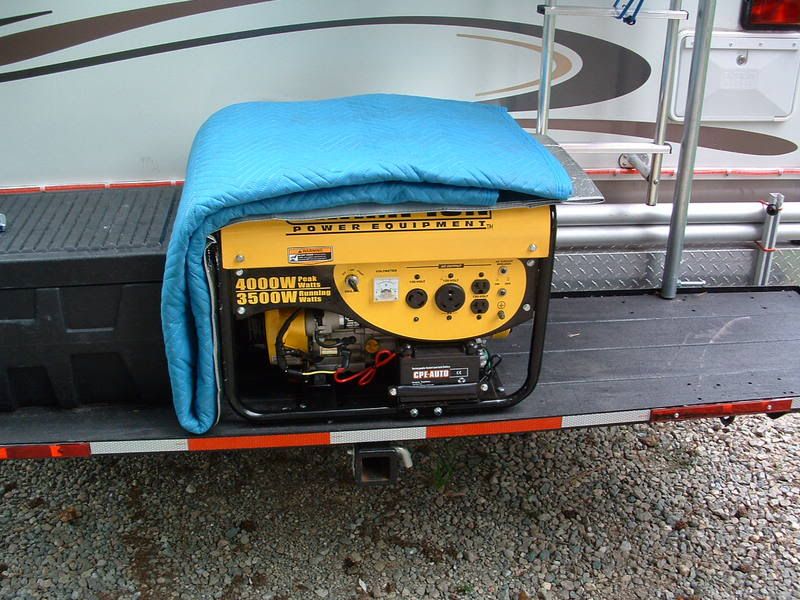
I then constructed a three sided enclosure with a top, keeping the alternator end open, out of ¼” fanfold polystyrene insulation board. It worked well in reducing sound levels to the 64 dB level on all but the open side. For a while I stored the thin insulation board under the mattress in the RV for use when the generator was needed. But, alas, it was a real hassle to drag it out and set it up. It also provided no real sound reduction benefit on the open end.
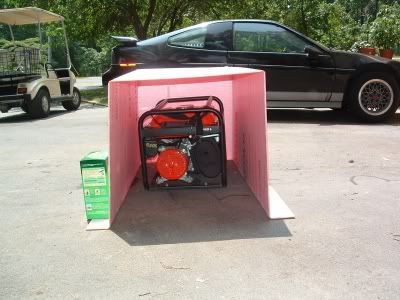
In September of ’06 I decided to make an enclosure for the entire generator. I settled on a rather elaborate design using numerous baffles to reduce sound paths and fans to assure adequate circulation of air for cooling the engine. I isolated the muffler with an ”L” shaped piece of aluminum and removed the gas tank. The major obstacles I encountered were providing power for the fans (the genset did not have a 12 volt DC output), designing a fuel delivery system for the now remote gas tank, radiant heat from the muffler raising internal temperatures – even with a heat shield – and the mass or bulk of the completed project. It was heavy, much larger than the original and in the long run way over built. Still, it did provide sound reduction on the order of 5 dB – a considerable amount when using the unit in an otherwise quite campground. I abandoned the enclosure later in the winter of ’07 believing I could come up with a better system.
In the Spring of ’07, before a trip back to the National Forest campground, I mounted the genset in the back of my truck (tow vehicle). I made some mounting skids from 2x4 lumber and constructed an exhaust pipe that exited through the roof of the truck’s fiberglass camper shell. This setup provided a significant reduction in sound but required opening a window on the camper shell and loosing some valuable storage space in the bed of the truck.

It proved to be only a temporary solution since I usually removed the camper shell during the summer so that the golf cart or jet ski could be placed in the truck bed and carried with us on our trips to the beach or lake.
By the summer of ’07, I had acquired two new Chinese built gensets. One was an electric start Champion 40008 capable of producing up to 4,000 watts of power at 120 volts, the other was a 7,500 peak watt unit utilizing an engine similar to the 13 HP Honda GX390. While the output of the smaller genset destined for RV use had been improved, the sound level had not. I had also become interested in using propane as an alternate fuel for gensets and successful converted both a Generac 5,500 and my new Champion 7,500 watt home back-up power generator to run on propane from an underground 300 gallon tank. Propane was the perfect fuel for my home generator; it did not go bad when stored for long periods of time and it was easy for me to store large quantities.
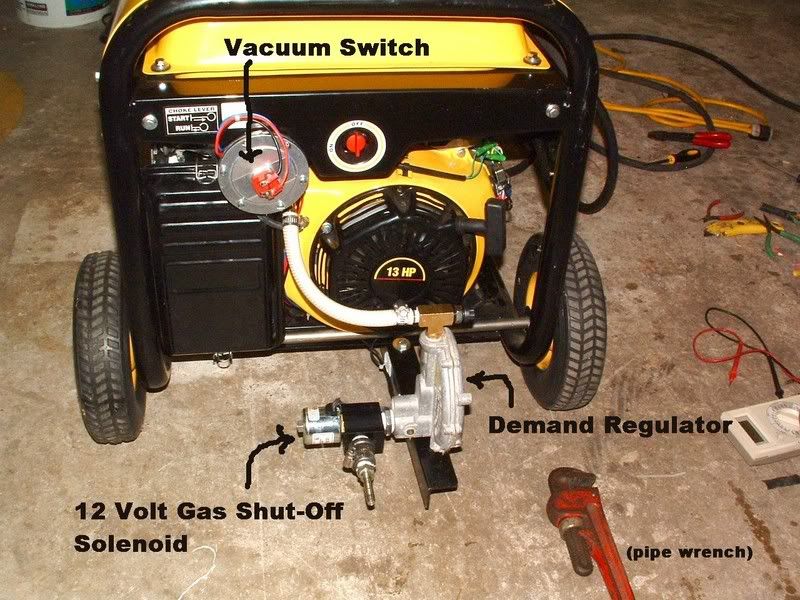
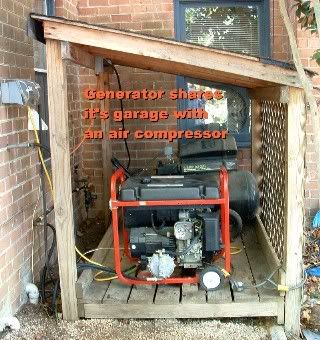
Both factors were extreme priorities after spending two weeks without commercial power after hurricane Isabel and one week after tropical storm Gaston. I required about 100 gallons of gasoline to keep the backup generator running during the aftermath of Isabel - no small feat in itself.
By late summer of ’07 my attention once again turned to some type of sound abatement enclosure for the Chinese built generator I used with the RV.
My previous attempts at building a sound abatement enclosure had taught me what NOT to do. I now knew that there were two priorities that would have to be met to insure some form of success:
1. The muffler had to be outside of the enclosure to lower internal temperatures. Efforts to shield the muffler inside the enclosure had been disappointing.
2. The fuel tank (or fuel source) could not be inside the enclosure. From a safety perspective, I was not comfortable with gasoline being inside a closed compartment.
I began to conduct some much needed research on the characteristics of sound waves along with their propagation and reproduction. Not surprisingly, the best source of information was found from elements of acoustical design. Buildings, auditoriums, speaker cabinets and even boom cars all draw from the same basic principles.
In designing a new enclosure, there were four basic principles that had to be considered; reflection, absorption, frequency and amplitude.
Through measurements made with a microphone, graphic equalizer and oscilloscope it was determined that the majority of sound energy was, as expected, under 5,000 Hz.
The amplitude had previously been established through measurements with a digital sound level meter and manufacturer’s data.
Since the sound frequencies were below 5,000 Hz, a small enclosure would do a better job of canceling the sound waves. Low frequencies have a longer wave length or period than high frequencies - the smaller the cabinet, the more attenuation of low frequency sound will occur. Audiophiles depend upon large diameter speakers, cabinets and tuned reflex ports for low frequency reproduction. Conversely, small diameter speakers and cabinets do a better job of reproducing high frequencies.
Anyone who has ever hooked up a set of speakers knows that they must be equally phased to reproduce sound properly. If one speaker is out of phase, or pulling the speaker cone in while the opposite speaker is pushing the cone out, the resultant sound waves will somewhat counter each other. Reflection of sound waves would be important in an enclosure to reduce sound pressure.
Absorption of sound waves turned out to be a considerably more complex than I originally believed. While it is true that materials with an open cellular structure can do an effective job of absorbing sound, caution must be exercised in selecting the material to assure there is sufficient density to cancel the effects of sound transmissions. Simply stated, when sound waves hit the surface of some materials the molecules in the material can also move or vibrate at the same rate as the sound pressure pushing against the material. Density, or thickness, of the material is a factor for consideration.
Add to all this my personal requirement that whatever I built to house the genset must not, in any way, compromise the original construction so that I could not at a later date return the genset to its original condition.
For my particular application, maintaining portability of the genset was not a priority. I had previously built a carrier on the back of my TT (with proper consideration for weights) and intended to permanently mount the genset square in the middle of the carrier. This would allow external mounting of the muffler under the carrier.
OK, let’s review both my personal requirements and needed elements to make the project successful:
1. Make no changes to the original genset that cannot be reversed.
2. Allow for adequate airflow to cool the engine and alternator, keeping the absolute maximum temperature under 175 degrees F.
3. Create a remote fuel source.
4. Move the muffler out of the enclosure.
5. Make the enclosure small.
6. Build the enclosure from materials that allow both reflection and absorption of sound waves.
Based on my findings, the ideal enclosure would be a perfect hemisphere (ball), the walls would be about 6” thick and made of both low density and high density material and there would be multiple small openings of less than 2” that could be tuned by inserting or withdrawing tubes (tuned port theory). Not a very practical item to build or use. A compromise enclosure containing all of the possible elements would have to be designed and built.
I did design and built such an enclosure and shared the construction/results on the forum.

Sound presssure at 21 feet was....

Professor Randy T. Agee
September 2007
About Technical Issues
Having RV issues? Connect with others who have been in your shoes.24,279 PostsLatest Activity: Jul 04, 2025