D_E_Bishop
Dec 11, 2013Explorer
Building a gen-turi style exhaust stack
Recently we were dry camping for an extended time and had to use the generator to recharge the batteries. My wife often smelled the exhaust and had me shut down. I got to thinking about a Gen-turi, but never having seen one was not too familiar with them other than what I had read here. When we got home, I did several searches on them and decided that for the price they cost from CAMCO, that I would build one.
I happened to see a factory model on display and took some measurements and discovered that the sweep was thin wall probably exhaust pipe material, 1.5” outside diameter and had a 9” radius to the sweep. I have seen a couple homemade units and they used stock 1 ¼” EMT with a 12” radius which caused the pipe to stand too far away from the sidewall for my taste. Having bent a bit of conduit and EMT, I knew it would be easy to make with the right material and bender. Who better to bend a piece of thin wall tubing for an exhaust pipe than a muffler shop. I went to a shop near us and for $15 they bent a piece of 1 ½” OD exhaust piping in an ell with a 9” radius and expanded one end to slip over my generator’s 1 ½” exhaust pipe.*
My next decision was, what to use for the stack. I decided to try a piece of three inch, triple wall drain pipe. It is like the pipe used in a leach field except without the drain holes. It is much lighter than PVC and it is clad with white plastic. I found the pipe at Lowe’s. It comes with a coupling glued on one end and it is a very tight fit so I decided to use standard PVC couplers.
Here is where I made my first mistake. Using my chop saw to insure square ends on the cuts, I cut the ten foot length of drain pipe into three equal length pieces. I failed to take into consideration that when the ell was attached to the pipe that it would make one piece 11” longer than the other two. My next stack will have three equal length pieces and will include the ell.
The CAMCO unit has three metal straps from the sweep to the pipe and I figured that would be adequate for mine. For the three straps I wanted a three foot length of, 1/16” by 5/8” mild steel stock. Not finding any 1/16” at Lowe’s I bought a piece of 1/8” by ½” stock.
I usually have a large selection of screws, nuts and washers in my shop and decided to use something I had on hand.
Now that I have the materials in shop it was time to layout the design and construction drawings. As stated, I had cut the pipe into three pieces and installed a coupling on two of the pieces. Now I had easier pieces to work with. The first thing I did was draw a circle on a piece of paper using the end of a piece of pipe of a template. Using my trusty compass I divided the circumference of the circle into six equal segments. I marked three alternating points of the six to use as transfer points to locate the straps on the pipe. Using a machinist’s square I drew longitudinal lines to show the centerlines if the straps on the pipe. My next drawing was a profile of the stack, straps and ell. I drew in full size and used the drawing of the assembly to bend the steel to fit, using a 4” bench vice and a ball peen hammer.
At this point I assembled the five pieces using tape and ty-raps(zip ties to most of you). I checked for fit and proper alignment using my trusty machinist and framing squares. My plan was to mount the straps to the stack using 8 or 10-32 SS carriage bolts with the heads on the inside of the stack and acorn nuts on the outside. Being unable to find the carriage bolts I changed my mind and decided to use some 10-32 pan head SS screws inserted from the inside and using acorn nuts on the outside. Trying to make this an inexpensive project to build, I changed from acorn nuts to hex nuts. The acorn nuts were over a dollar apiece for a cost of slightly over $10, way too much as long as I had a good supply of hex nuts on hand to use.*
Now all that was left was to mount the straps to the pipe and have them welded to the ell. I dry fit all the pieces and found the expanded end of the ell was not large enough, so back to the muffler shop for some work. Now that the pieces all fit, I had the muffler shop weld the straps to the ell.
I disassembled the straps and ell from the stack, sanded and wire brushed, primed and painted them with high temp engine paint. I assembled and installed the home built exhaust stack on the motorhome for the next phase of design and fabrication. Most guys don’t want to drill holes and mount brackets to the side of their rigs and suction cups seem to be the common alternative. Harbor freight to the rescue, they have at least five different suction cup available that would work. One or two of these, a couple of bungees and a solid but removable mounting system is born. I decided to use a 4 ½” suction cup, one bungee and a plywood standoff to secure the stack in its’ vertical position and away from the side of the MoHo. The suction cup is easy to position, attach and remove from the side of the MoHo or window and does not leave any marks or scratch the finish or glass.
I did not feel that I needed to support the stack with the suction cup as my exhaust pipe is securely mounted to the rig like most generator exhausts are by using a typical muffler hanger available at auto parts stores. The finished assembly leans toward the side of the MoHo and I decided that I needed a standoff to make it parallel to the side of the rig. It is made out of 3/8” Baltic birch plywood and painted to match the stack. The standoff sits against the orange suction cup I use to attach the bungees that help keep the stack in place. Each rig is different and methods of mounting will differ accordingly. So for about $60, I have my home made generator exhaust stack which if I do say so myself looks like it was factory made.
There are several photographs and a complete parts list as well as a list of tools I used in the build. All are tools I had in my shop and you could use what you have on hand, like substituting a hand saw for the chop saw.
While is does not seem to be necessary, I have thought about applying red and white stripped reflectorized tape to the stack between the straps to indicate using caution. Then again “if it ain’t broke, don’t fix it”.
*On note;
While dry fitting the stack to my MoHo, I observed that many newer rigs have smaller generator exhaust pipes. I asked the owner of the muffler shop about bushings to enlarge out to the proper OD. He said no problem, just give him the measurements and for a couple of bucks he would make them. They are also available from CAMCO as a second generator kit.
I did not like the look or feel of the machine screws and nuts, so I changed them back to my original design. I found 3/16” – 24 X ¾” carriage bolts and acorn nuts at my local hardware store for a reasonable price.
TOOL LIST
10” chop saw
Drill press
Drill motor
Several different drill bits
Screwdrivers
Spin tights
Tape, Ty-Raps and hose clamps
Hacksaw
File, mill bastard
Marking pens
Center punch
Ball peen hammer
4” Vise
Machinist and framing squares
MATERIALS LIST
1 - 10’ length of 3” drain pipe
1 - 3’ length of 1/8’ X ½” X 3’ mild steel stock
2 – 3” PVC couplings
1 - 1 ½” OD ell, 9” sweep, expanded on one end to fit over 1 ½’ exhaust pipe
9 - 3/6” – 24 X ¾” carriage bolts and acorn nuts.
1 – 4 ½” HF Quick release Suction cup
1 – 4” X 5”, 3/8 “ plywood
The finished exhaust stack cost me about $60 and took about six hours of labor. I could have purchased one for about $110 and $15 shipping for a net savings of $65. If I had to put a price on my labor and hours I spent shopping, it would have been a lot cheaper to buy one and have it shipped to my house in a nice carrying case. However, I had a lot of fun doing it and it was a break from working on the house remodeling, which was priceless.
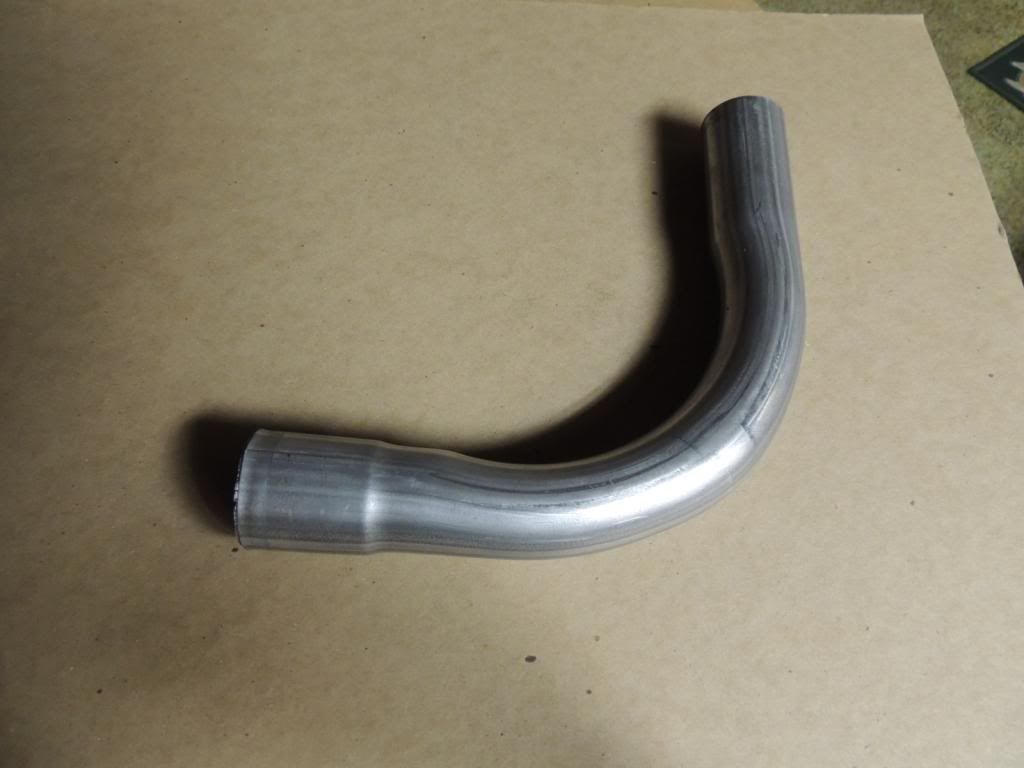
This is the ell made by the muffler shop
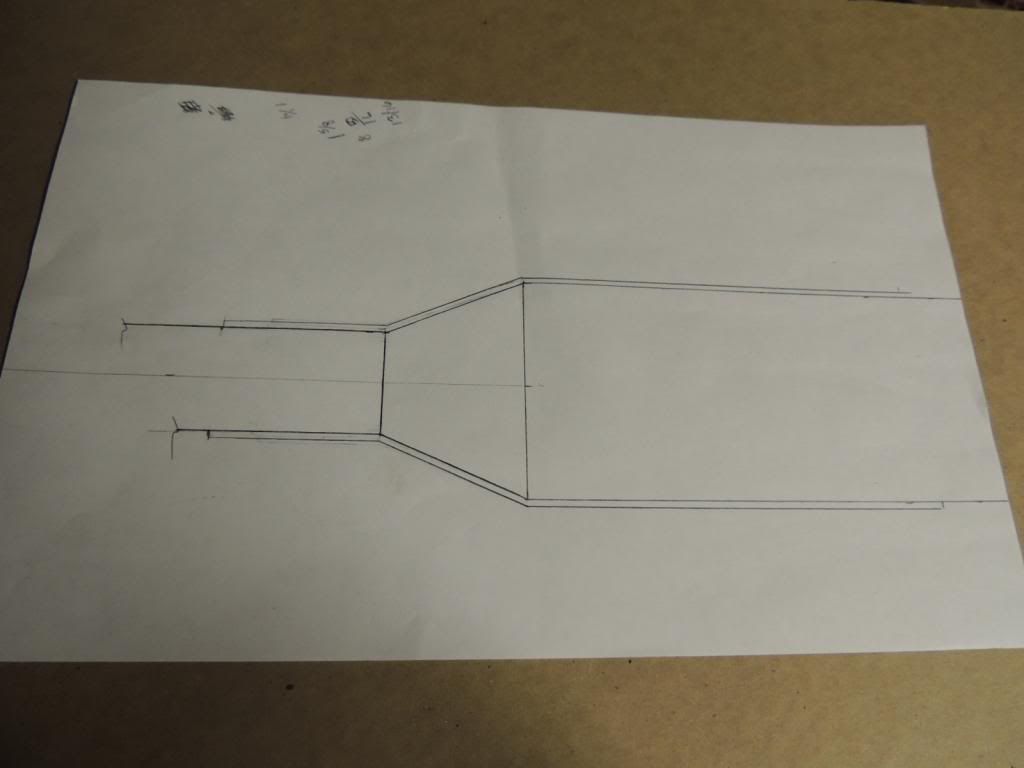
This is a drawing for bending the straps
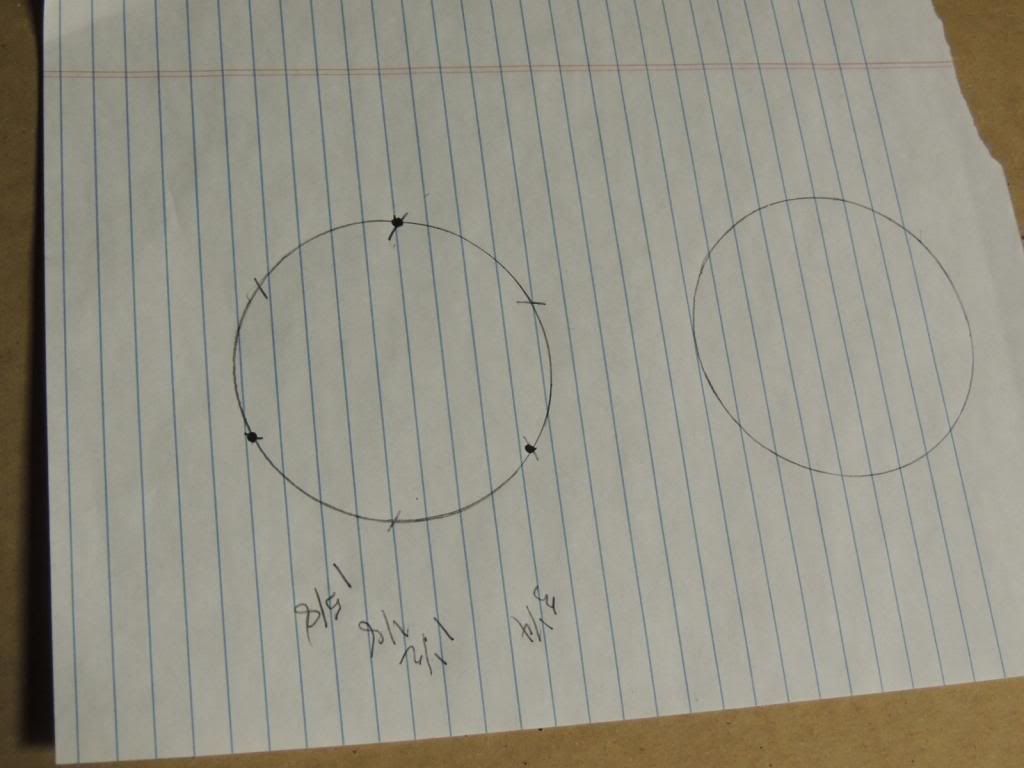
I divided the circumference of the pipe into six then 3 equal sections to locate straps
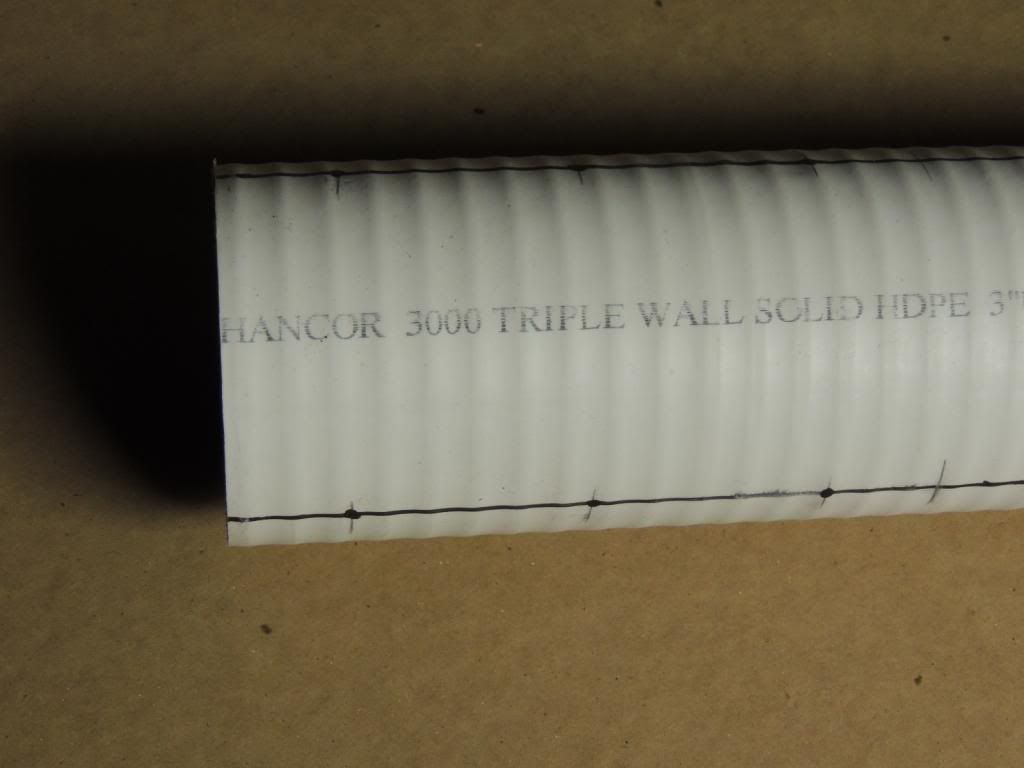
The pipe with the center lines for the straps
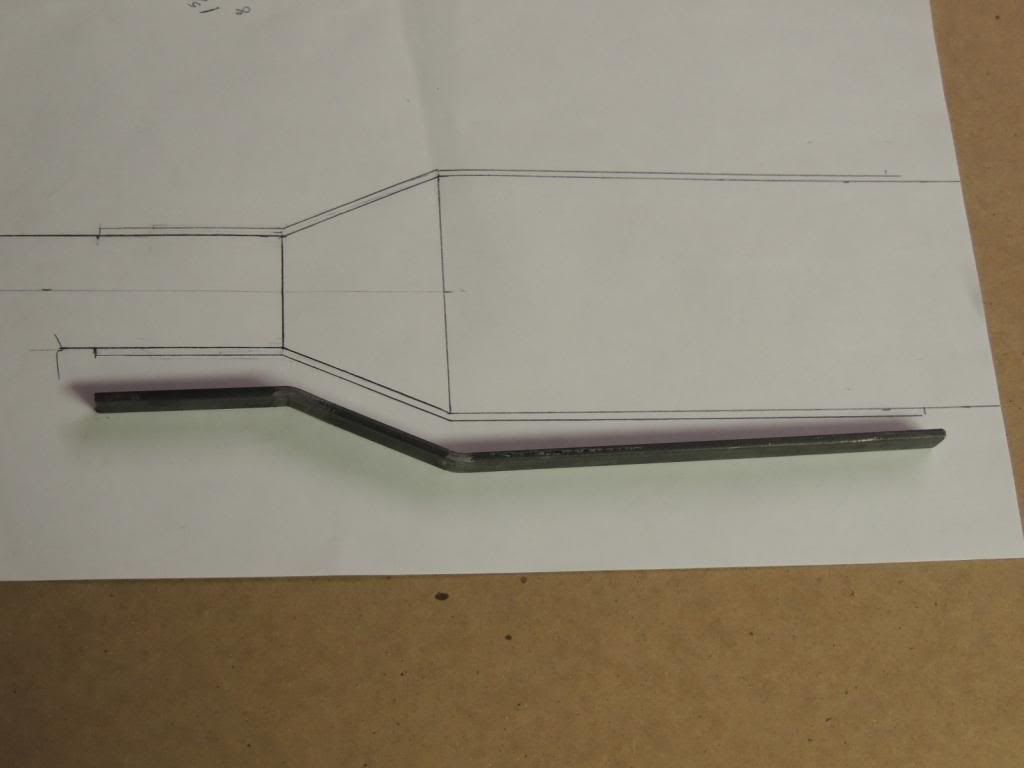
This compares the bends in the strap to the drawing
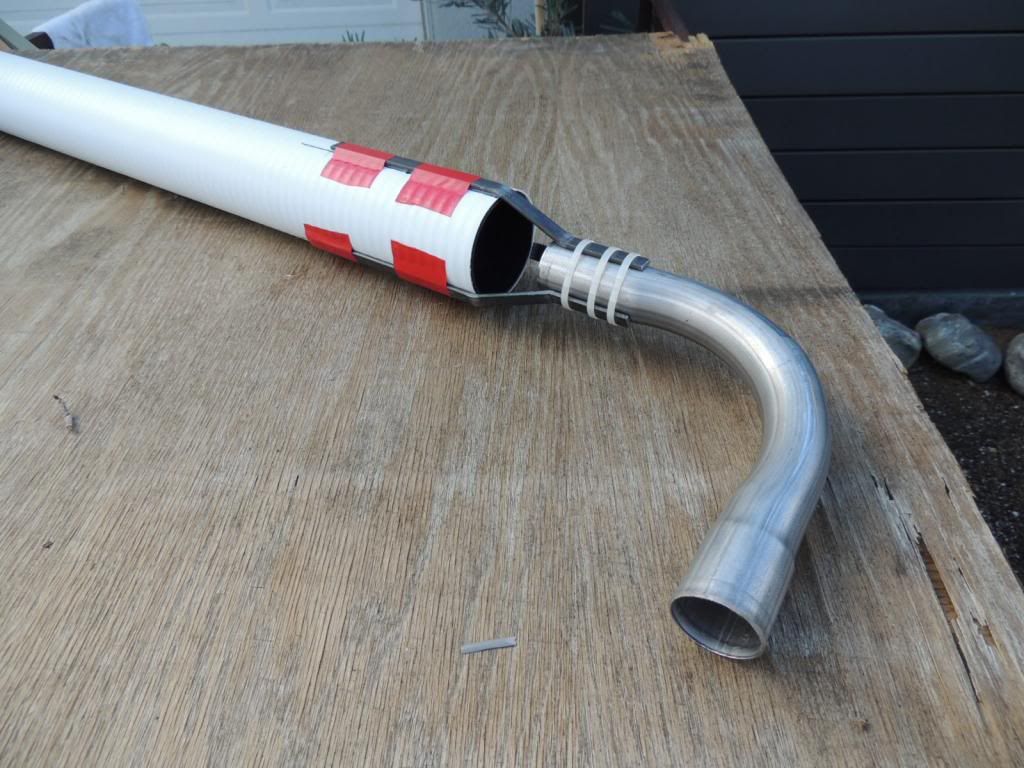
Here the straps are taped to the pipe and the ell is ty-rapped to the ell
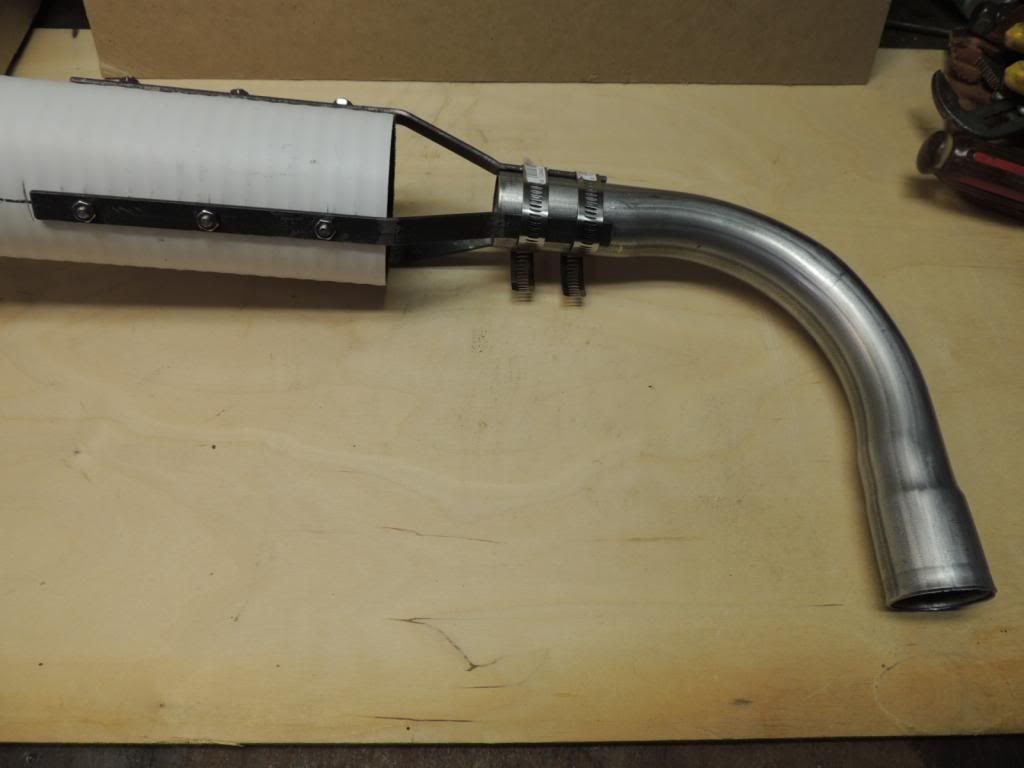
Here the straps have been drilled and mounted to the pipe and ell is held in place with hose clamps so it can be fitted to the generator exhaust pipe, notice the plain hex nuts
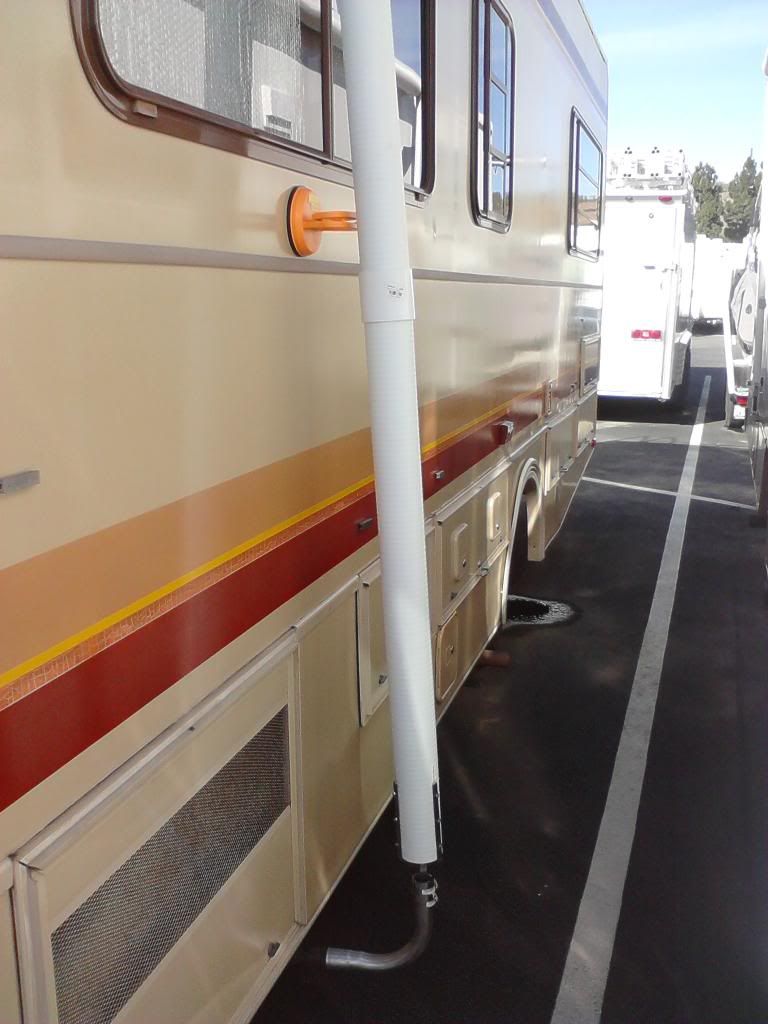
This picture is of the stack dry fitted to the generator
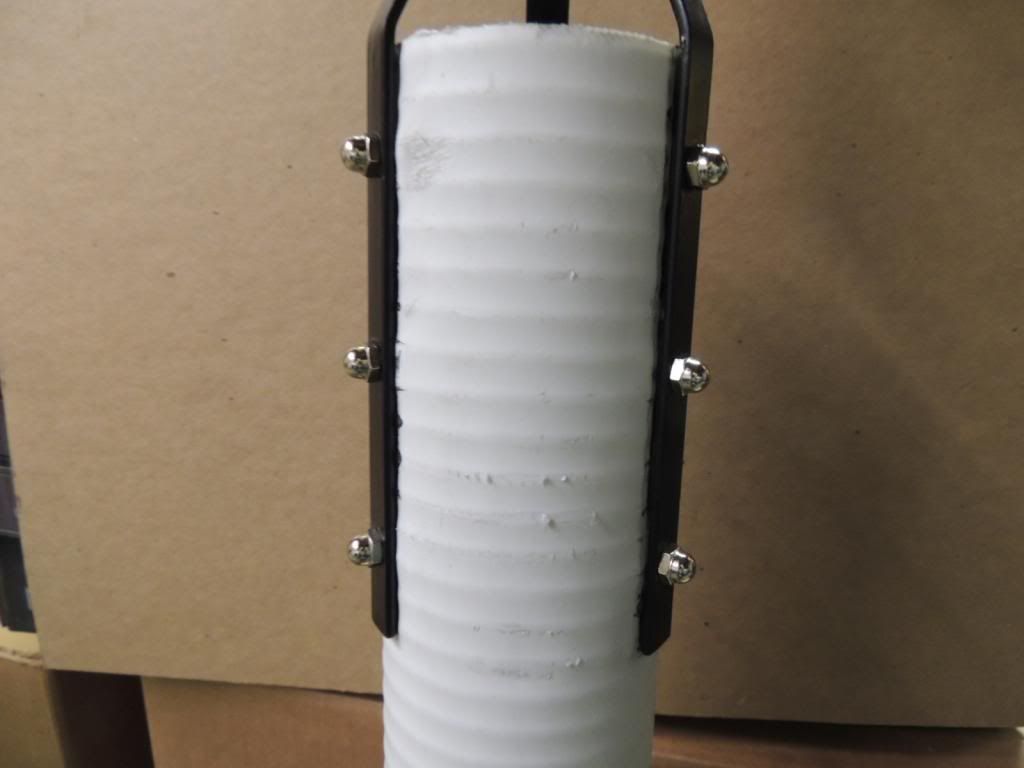
This is after I changed the nuts to acorn nuts and painted the straps and ell
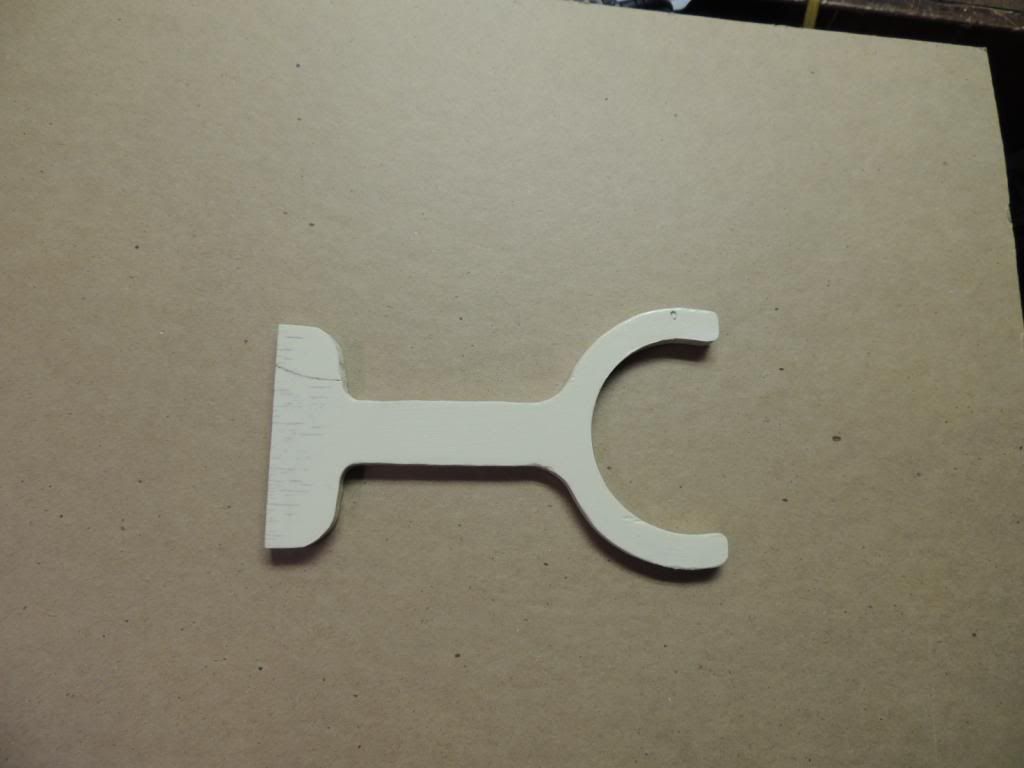
The plywood standoff
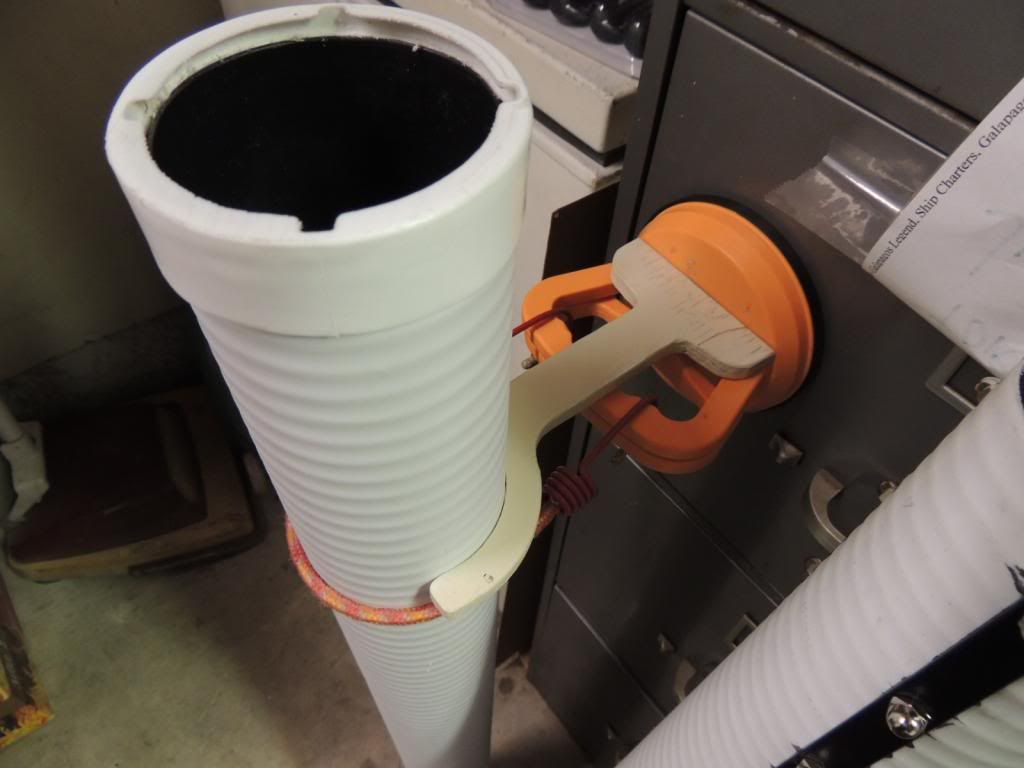
Suction cup, standoff and bottom section of stack attached to file cabinet with bungee and suction cup
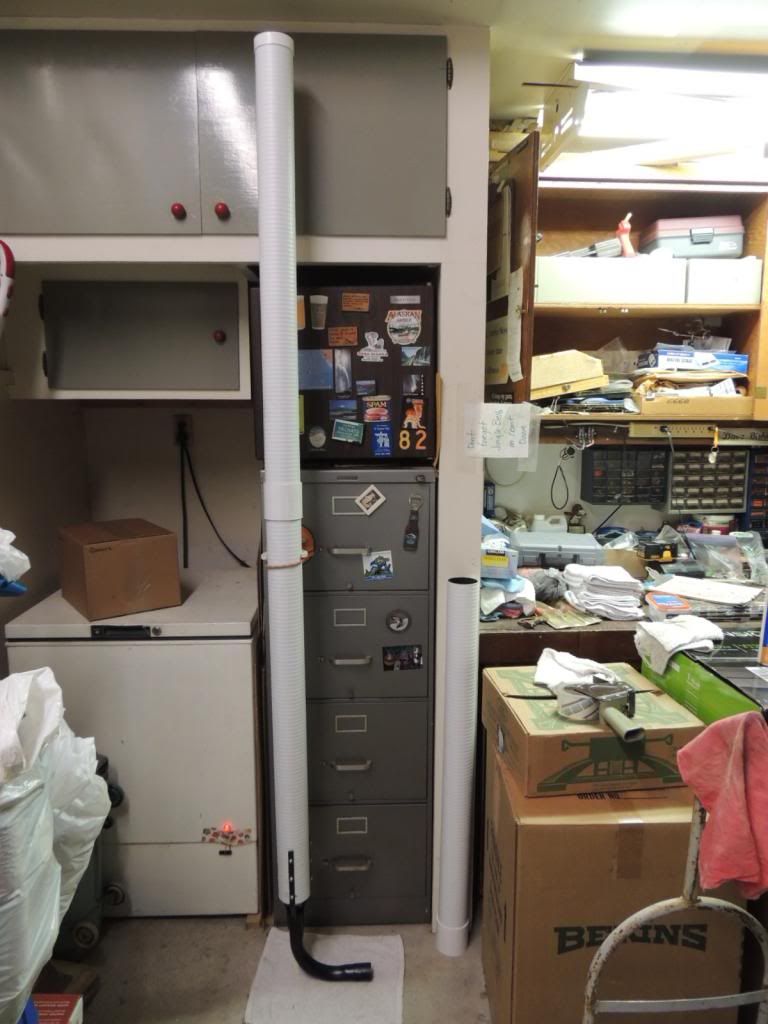
Two sections of the stack held to the file cabinet with the bungee and standoff
I happened to see a factory model on display and took some measurements and discovered that the sweep was thin wall probably exhaust pipe material, 1.5” outside diameter and had a 9” radius to the sweep. I have seen a couple homemade units and they used stock 1 ¼” EMT with a 12” radius which caused the pipe to stand too far away from the sidewall for my taste. Having bent a bit of conduit and EMT, I knew it would be easy to make with the right material and bender. Who better to bend a piece of thin wall tubing for an exhaust pipe than a muffler shop. I went to a shop near us and for $15 they bent a piece of 1 ½” OD exhaust piping in an ell with a 9” radius and expanded one end to slip over my generator’s 1 ½” exhaust pipe.*
My next decision was, what to use for the stack. I decided to try a piece of three inch, triple wall drain pipe. It is like the pipe used in a leach field except without the drain holes. It is much lighter than PVC and it is clad with white plastic. I found the pipe at Lowe’s. It comes with a coupling glued on one end and it is a very tight fit so I decided to use standard PVC couplers.
Here is where I made my first mistake. Using my chop saw to insure square ends on the cuts, I cut the ten foot length of drain pipe into three equal length pieces. I failed to take into consideration that when the ell was attached to the pipe that it would make one piece 11” longer than the other two. My next stack will have three equal length pieces and will include the ell.
The CAMCO unit has three metal straps from the sweep to the pipe and I figured that would be adequate for mine. For the three straps I wanted a three foot length of, 1/16” by 5/8” mild steel stock. Not finding any 1/16” at Lowe’s I bought a piece of 1/8” by ½” stock.
I usually have a large selection of screws, nuts and washers in my shop and decided to use something I had on hand.
Now that I have the materials in shop it was time to layout the design and construction drawings. As stated, I had cut the pipe into three pieces and installed a coupling on two of the pieces. Now I had easier pieces to work with. The first thing I did was draw a circle on a piece of paper using the end of a piece of pipe of a template. Using my trusty compass I divided the circumference of the circle into six equal segments. I marked three alternating points of the six to use as transfer points to locate the straps on the pipe. Using a machinist’s square I drew longitudinal lines to show the centerlines if the straps on the pipe. My next drawing was a profile of the stack, straps and ell. I drew in full size and used the drawing of the assembly to bend the steel to fit, using a 4” bench vice and a ball peen hammer.
At this point I assembled the five pieces using tape and ty-raps(zip ties to most of you). I checked for fit and proper alignment using my trusty machinist and framing squares. My plan was to mount the straps to the stack using 8 or 10-32 SS carriage bolts with the heads on the inside of the stack and acorn nuts on the outside. Being unable to find the carriage bolts I changed my mind and decided to use some 10-32 pan head SS screws inserted from the inside and using acorn nuts on the outside. Trying to make this an inexpensive project to build, I changed from acorn nuts to hex nuts. The acorn nuts were over a dollar apiece for a cost of slightly over $10, way too much as long as I had a good supply of hex nuts on hand to use.*
Now all that was left was to mount the straps to the pipe and have them welded to the ell. I dry fit all the pieces and found the expanded end of the ell was not large enough, so back to the muffler shop for some work. Now that the pieces all fit, I had the muffler shop weld the straps to the ell.
I disassembled the straps and ell from the stack, sanded and wire brushed, primed and painted them with high temp engine paint. I assembled and installed the home built exhaust stack on the motorhome for the next phase of design and fabrication. Most guys don’t want to drill holes and mount brackets to the side of their rigs and suction cups seem to be the common alternative. Harbor freight to the rescue, they have at least five different suction cup available that would work. One or two of these, a couple of bungees and a solid but removable mounting system is born. I decided to use a 4 ½” suction cup, one bungee and a plywood standoff to secure the stack in its’ vertical position and away from the side of the MoHo. The suction cup is easy to position, attach and remove from the side of the MoHo or window and does not leave any marks or scratch the finish or glass.
I did not feel that I needed to support the stack with the suction cup as my exhaust pipe is securely mounted to the rig like most generator exhausts are by using a typical muffler hanger available at auto parts stores. The finished assembly leans toward the side of the MoHo and I decided that I needed a standoff to make it parallel to the side of the rig. It is made out of 3/8” Baltic birch plywood and painted to match the stack. The standoff sits against the orange suction cup I use to attach the bungees that help keep the stack in place. Each rig is different and methods of mounting will differ accordingly. So for about $60, I have my home made generator exhaust stack which if I do say so myself looks like it was factory made.
There are several photographs and a complete parts list as well as a list of tools I used in the build. All are tools I had in my shop and you could use what you have on hand, like substituting a hand saw for the chop saw.
While is does not seem to be necessary, I have thought about applying red and white stripped reflectorized tape to the stack between the straps to indicate using caution. Then again “if it ain’t broke, don’t fix it”.
*On note;
While dry fitting the stack to my MoHo, I observed that many newer rigs have smaller generator exhaust pipes. I asked the owner of the muffler shop about bushings to enlarge out to the proper OD. He said no problem, just give him the measurements and for a couple of bucks he would make them. They are also available from CAMCO as a second generator kit.
I did not like the look or feel of the machine screws and nuts, so I changed them back to my original design. I found 3/16” – 24 X ¾” carriage bolts and acorn nuts at my local hardware store for a reasonable price.
TOOL LIST
10” chop saw
Drill press
Drill motor
Several different drill bits
Screwdrivers
Spin tights
Tape, Ty-Raps and hose clamps
Hacksaw
File, mill bastard
Marking pens
Center punch
Ball peen hammer
4” Vise
Machinist and framing squares
MATERIALS LIST
1 - 10’ length of 3” drain pipe
1 - 3’ length of 1/8’ X ½” X 3’ mild steel stock
2 – 3” PVC couplings
1 - 1 ½” OD ell, 9” sweep, expanded on one end to fit over 1 ½’ exhaust pipe
9 - 3/6” – 24 X ¾” carriage bolts and acorn nuts.
1 – 4 ½” HF Quick release Suction cup
1 – 4” X 5”, 3/8 “ plywood
The finished exhaust stack cost me about $60 and took about six hours of labor. I could have purchased one for about $110 and $15 shipping for a net savings of $65. If I had to put a price on my labor and hours I spent shopping, it would have been a lot cheaper to buy one and have it shipped to my house in a nice carrying case. However, I had a lot of fun doing it and it was a break from working on the house remodeling, which was priceless.
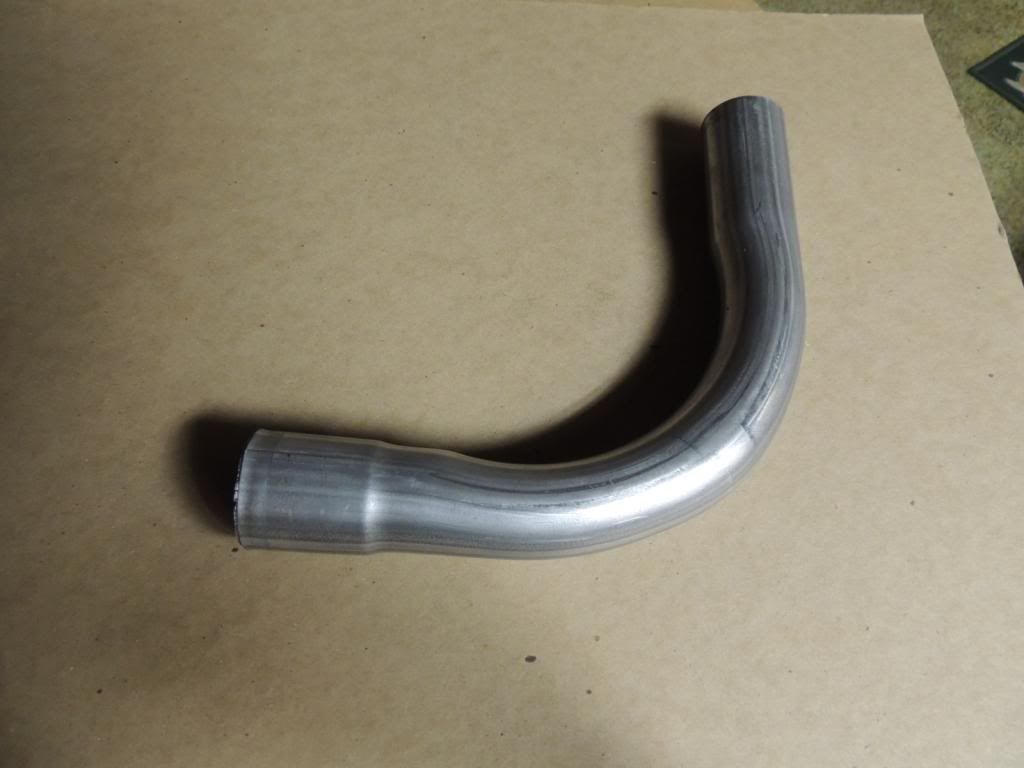
This is the ell made by the muffler shop
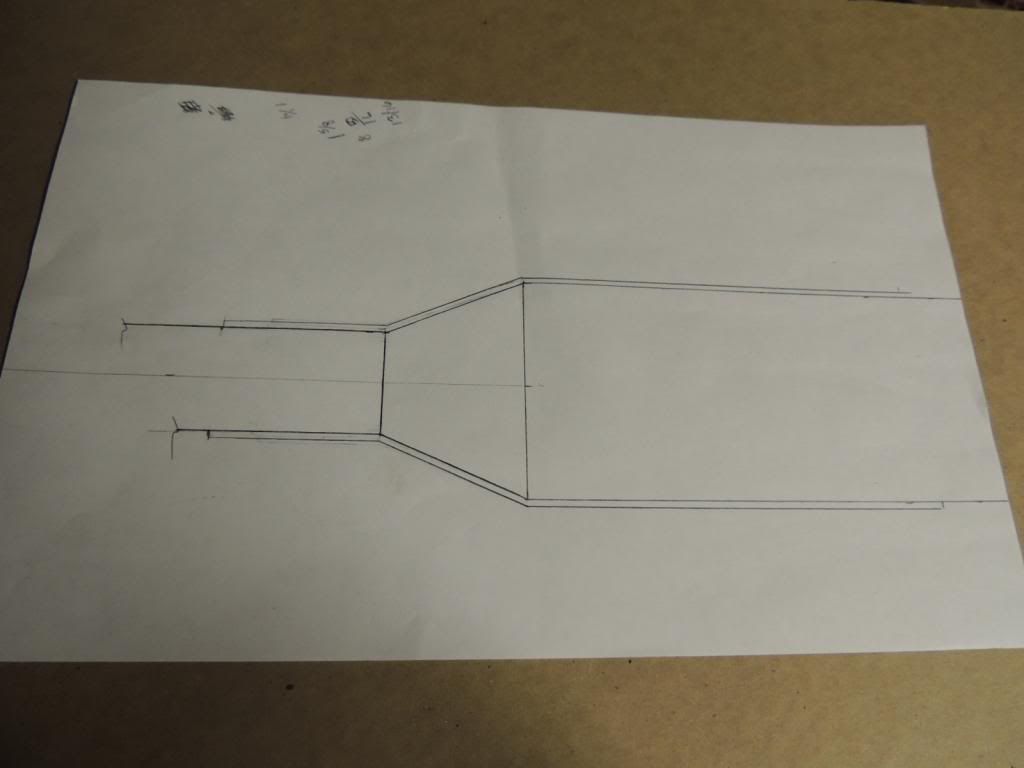
This is a drawing for bending the straps
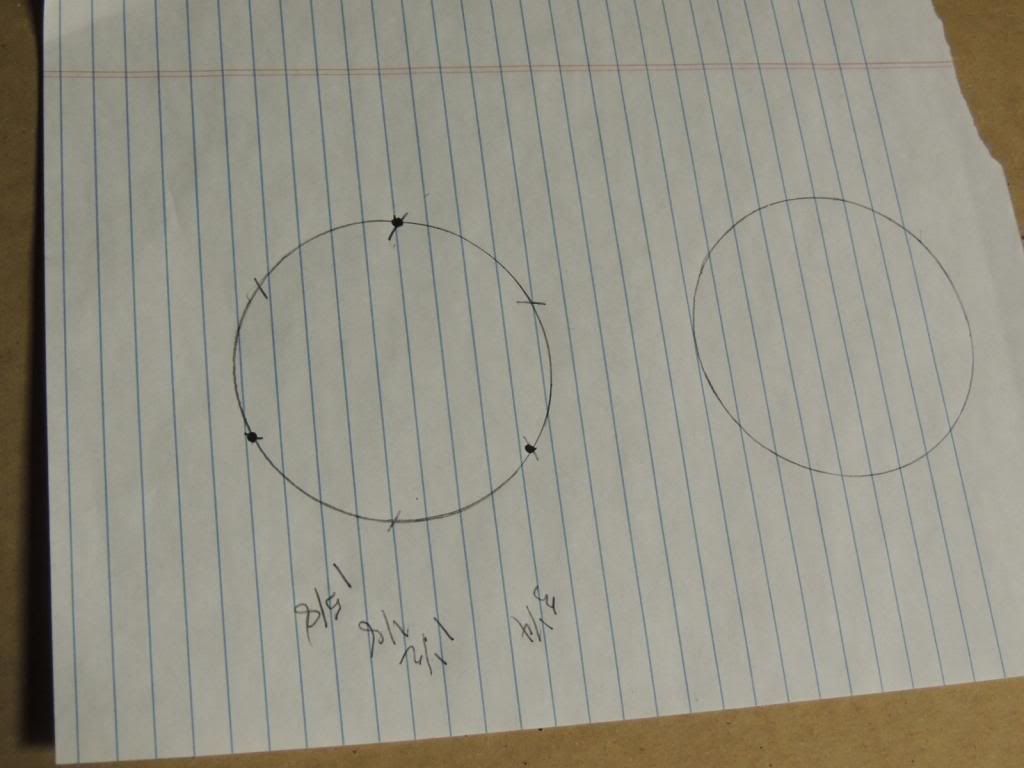
I divided the circumference of the pipe into six then 3 equal sections to locate straps
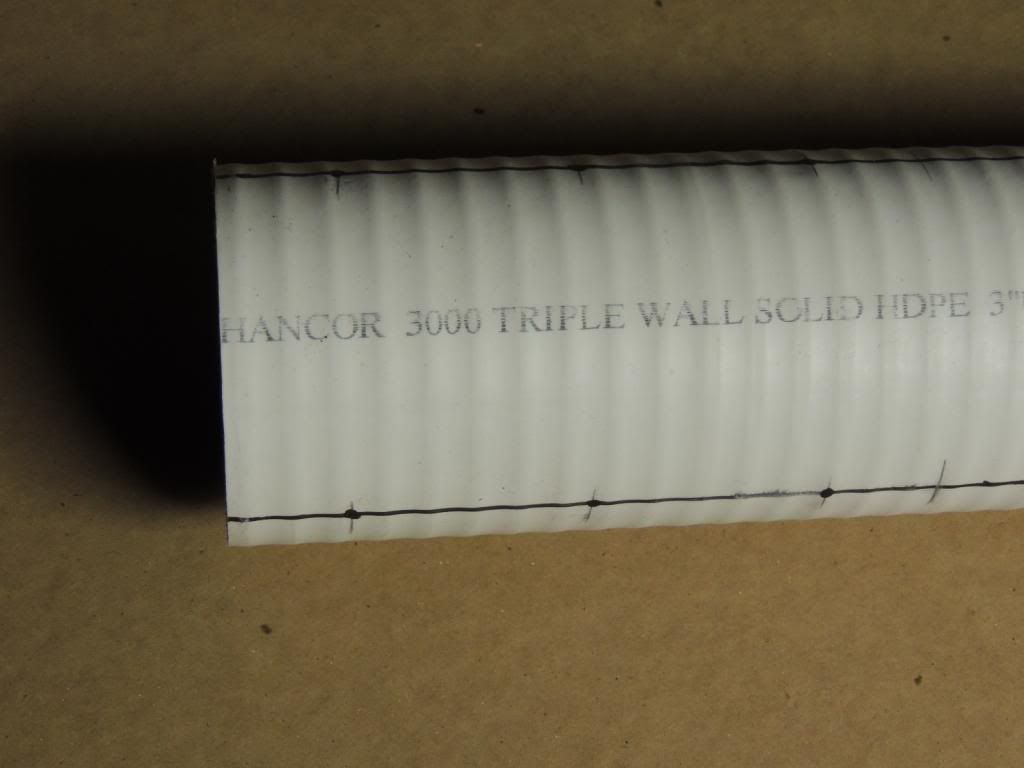
The pipe with the center lines for the straps
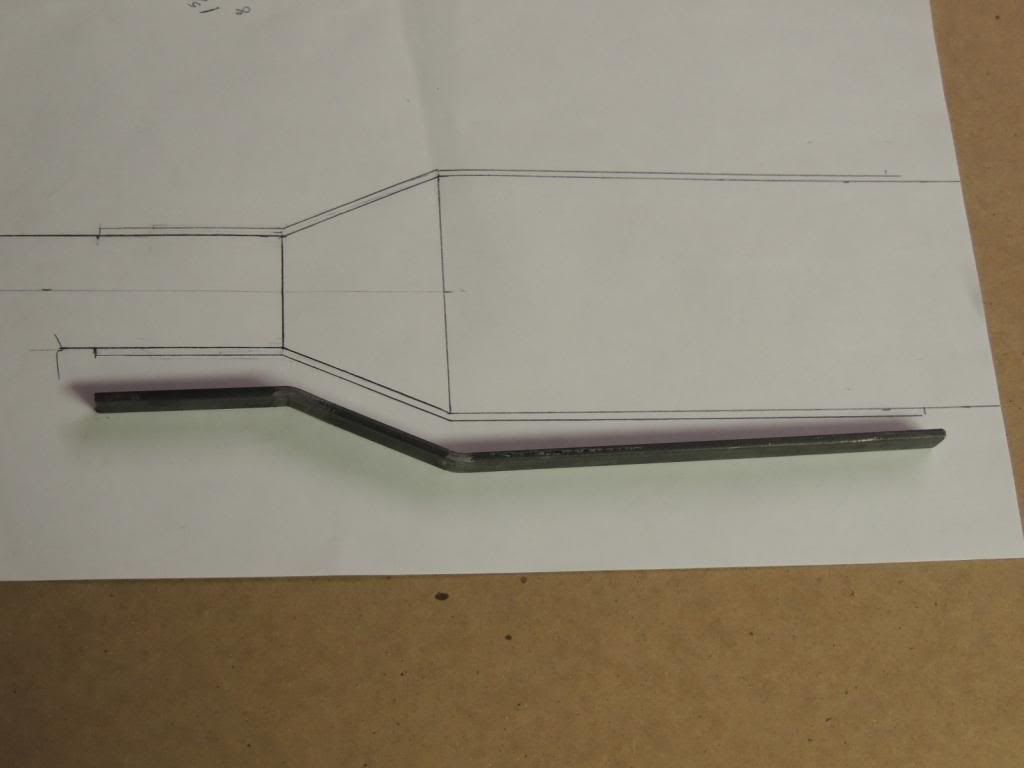
This compares the bends in the strap to the drawing
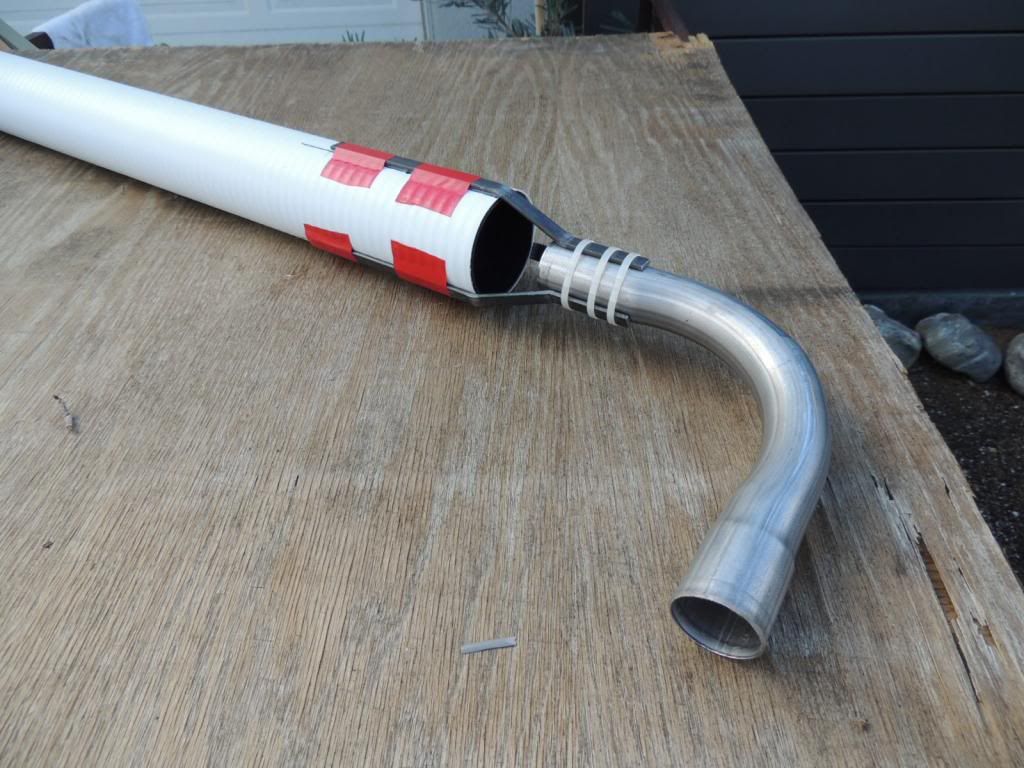
Here the straps are taped to the pipe and the ell is ty-rapped to the ell
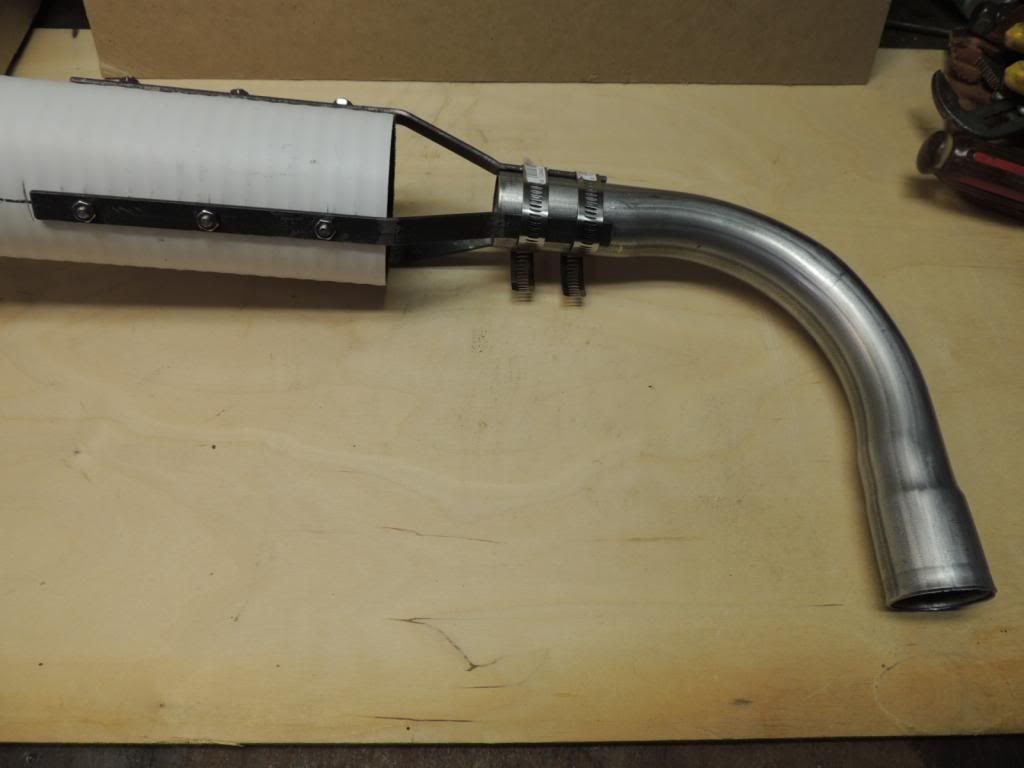
Here the straps have been drilled and mounted to the pipe and ell is held in place with hose clamps so it can be fitted to the generator exhaust pipe, notice the plain hex nuts
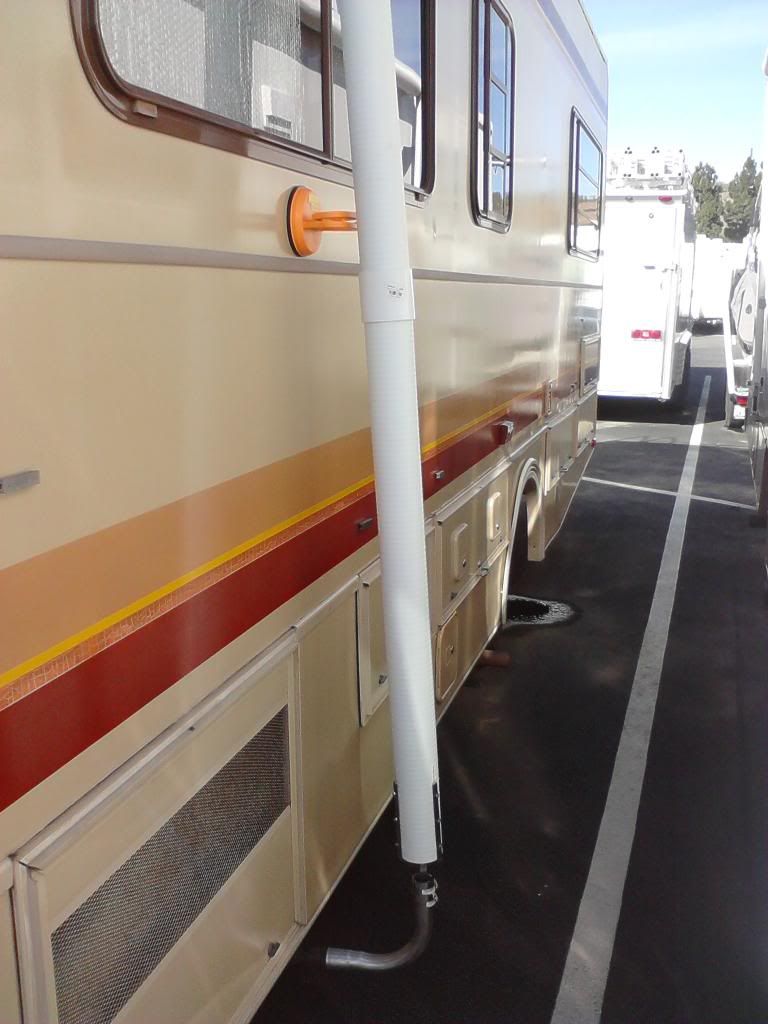
This picture is of the stack dry fitted to the generator
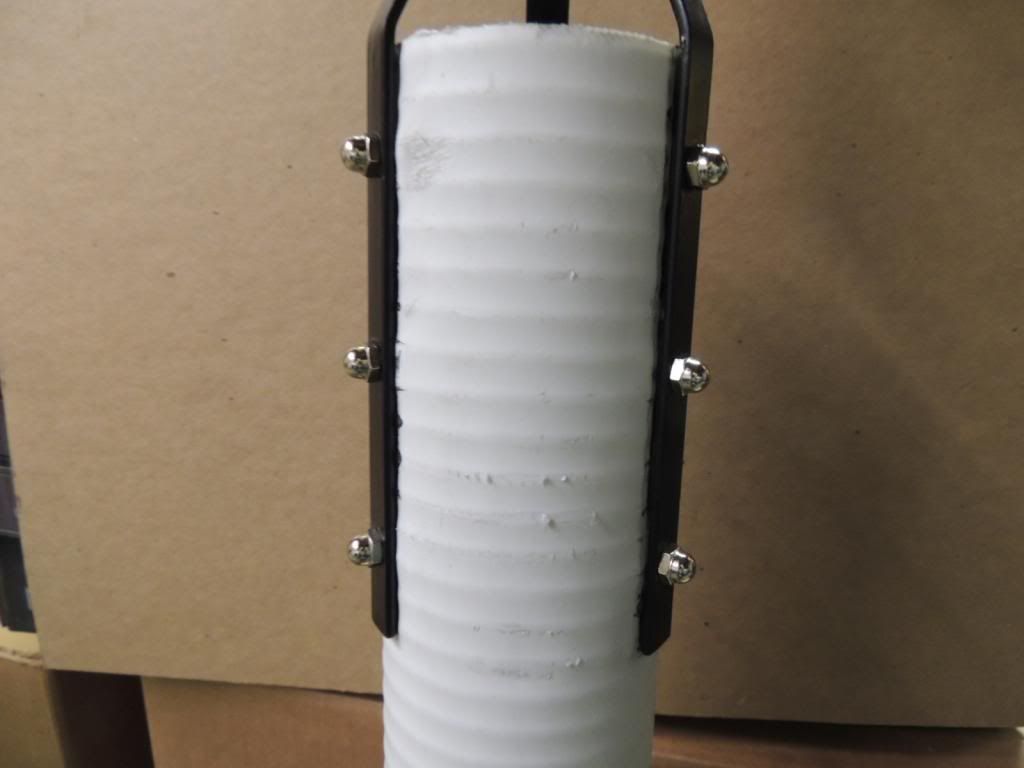
This is after I changed the nuts to acorn nuts and painted the straps and ell
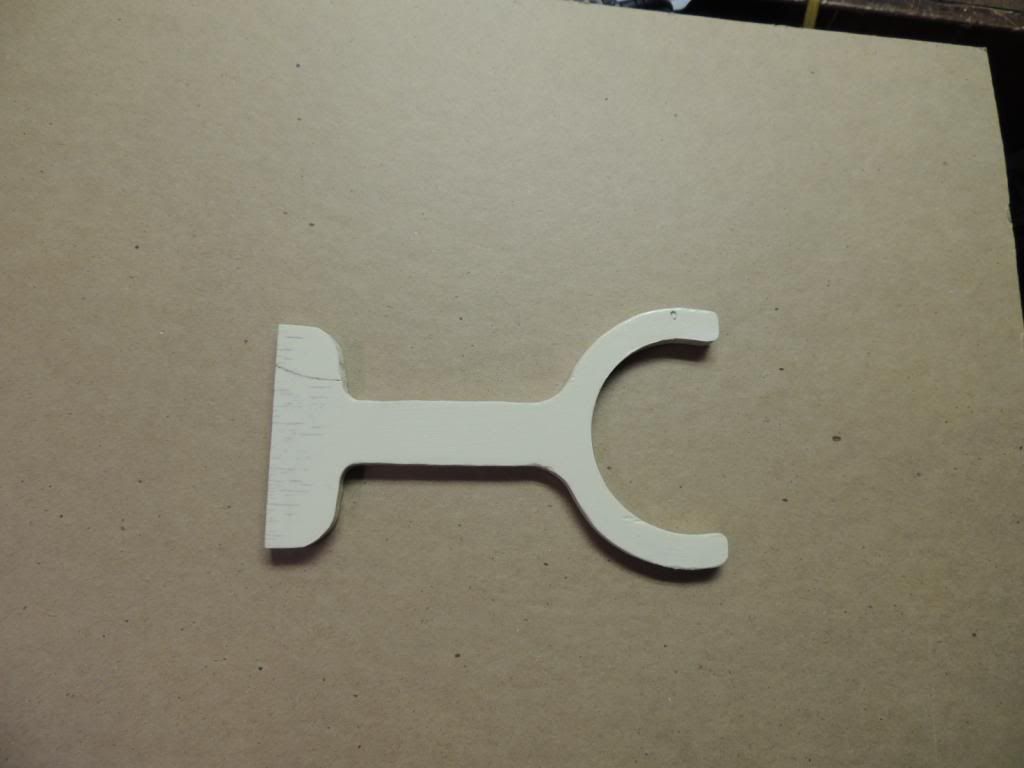
The plywood standoff
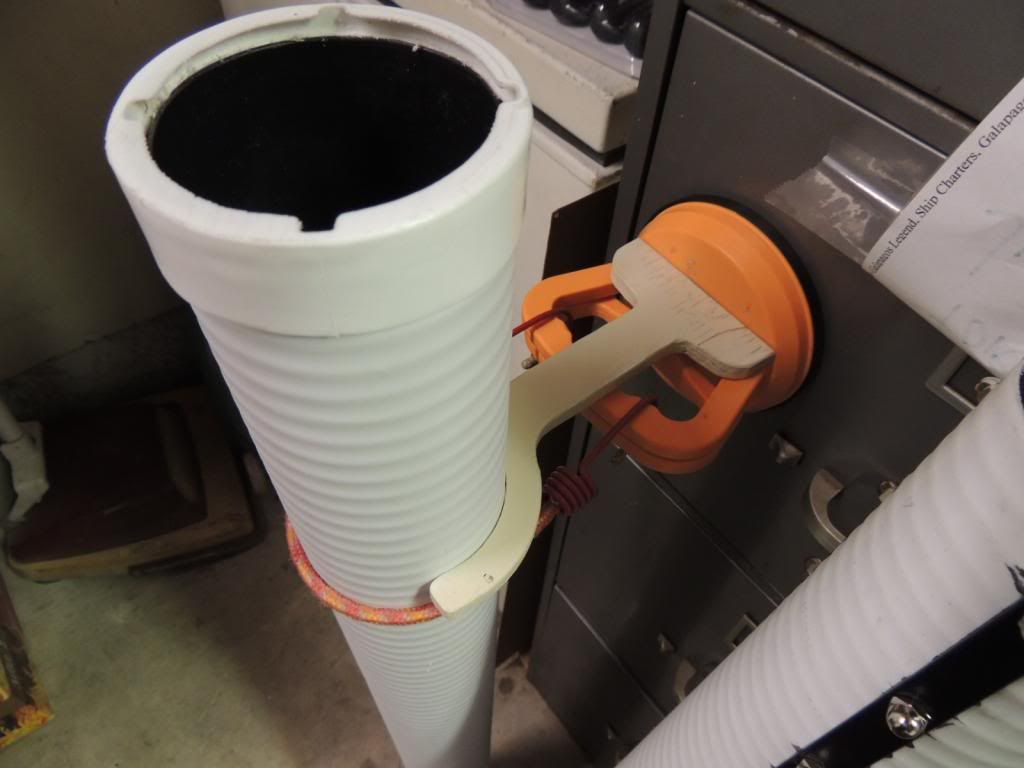
Suction cup, standoff and bottom section of stack attached to file cabinet with bungee and suction cup
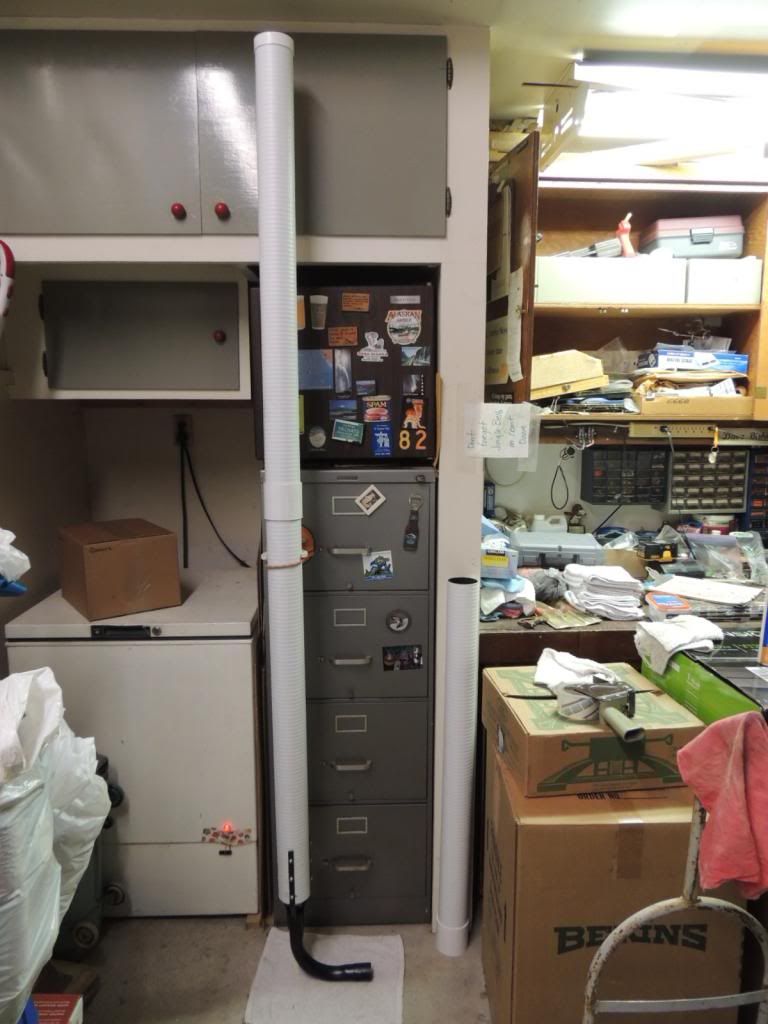
Two sections of the stack held to the file cabinet with the bungee and standoff