Hey recycler, it's been a couple months and we're well into May now buddy: how's the glassing going ?
First up, the furnace.
This is a unit made by now-defunct Flame Master in Edmonton so forget about finding any kind of info for it. (I think) the process has given me a pretty good feel for what makes these things tick.
The patient (click on pics for bigger):
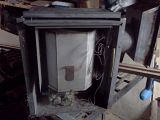
The problem was no fire: I had only a miniscule amount of gas flow and even that was intermittent. The ducting on this is all wrong for my build and I think it would be overkill in my little trailer anyway but I had the thing, I had the bench clear, so why not dive in and see if I could get it going...
I could go into a long tale of what I checked and what I found, but the end result was that the orifice for the pilot flame was plugged solid. I soaked it in mineral spirits for a day or so, blew it out, now it runs great.
This video is with the bottom plate removed for testing. The Tcouple is sitting in place just to hold the valve open (again, just for testing).
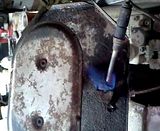
I have a few more pix so if anyone's interested in them or the steps I went through, just ask.
Now, to get back on track:
I haven't been too happy with trying to shoehorn the stove/oven in and I've been thinking pretty critically about how I'll be using the trailer. Given that some of my favorite spots get stupidly hot during the summer
๐ I like the option of being able to take the cooking outside of where we sleep. To that end, I have remodeled the galley a little bit to make space for a two burner stove rather than the three-burner-plus-oven hob over the water tank. That will give me a bit of storage below and will save me probably 50 lbs...even with half a dozen canisters rolling around. So it looks like I'll be trying out one of those Coleman ovens when it comes time for the breakfast bikkies !

I still need to get rid of the heat and humidity of cooking and it didn't make sense to use the range hood since it goes with the stove. Besides, I can do better than a squirrel cage and an incandescent lamp with my 12V...like a PC fan and fluorescent or LED cooktop lighting. As it is, the range hood I have is meant for a vertical wall where mine needs to hit an angled wall section. I could just extend the ducting, but then it would be proud of the edge of the counter: an ergonomic no-no. The solution: Bah, I'll just make one !
First I had to make up a pattern for the end plates. Mostly I just needed the angle from the sidewall to the canted upper portion where it meets the roof (which I could get with a T-bevel and a few measurements) but I thought I'd detail a neat trick for pattern making:
Start with a sheet of 1/8" doorskin ($5-10) and rip it into 1" strips. I use a bit of the stuff so I always have scraps to rip for patterns, then 'repurpose' them into stir sticks for resin. Add a hot glue gun and you're off to the races.
This is where I'm starting - I want the range hood to start at the corner where the sidewall meets the upper section and go up from there.
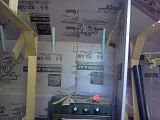
I laid in the first strip, glued to the temporary foam gusset in the back, leveled it across the bulkhead to establish the bottom line and glued in the front.
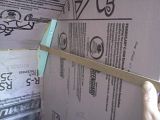
Keep following the contours you want to match by gluing in more 'sticks' and presto: one robust, ready-to-trace pattern that matches exactly.
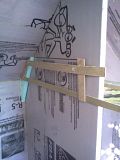
The finished pattern, cleaned up and ready for action.
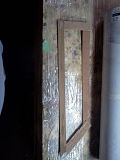
I picked up 5' of roll flashing and that's as far as I've gotten with it so far.
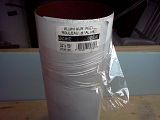
My plan is to make up the two ends (sides) and pop rivet them to the top. I will seal the whole thing (though I haven't yet decided with what - prob just SikaFlex) and will make it so that the end plates don't show the rivets, since they will be visible but the top won't.
Question here for winter campers: do you find that the range hood is a source of drafts ? With a 3" square duct directly outside, it seems like it would sink cold air right into the trailer.
I'm thinking of something like a dryer vent, but one doesn't normally see anything like that on RVs (just louvered covers) so it can't be that big an issue....right ?
I'd much rather have the duct protrude an eighth or so and cover it with a clamshell.

I've also been working on the door frame, having lined it with cedar and glassed the outer face. Being only a couple inches wide, the inner face will get glassed with the inside wall when I join it all together but I a bit of extra cloth on the outside won't be a bad thing. I may have to rip the door down a little as I build the glass up, but I allowed for that when I was making the door. This is the frame as cut out of the wall for glassing with the door wedged in.
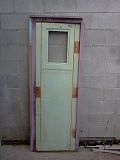
And laid out on the bench with the fir threshold clamped down. Once I got it all square, I ran drywall screws through the underside of the bench (1/2" ply) and into the foam to hold it. No fuss, no muss, no clamps to work around nor screws to pull as you go.....just remember to pull them before trying to flip it over to do the other side !
๐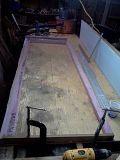
Then I let in the blocks and glued them with PU glue. Once that had hardened, I glued in the cedar strips (the actual wood jamb) with thickened epoxy. I wrapped the outside edge of the door in packing tape so the epoxy wouldn't stick to it and used it to hold the strips in place until the epoxy set up.
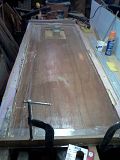
The 'rough opening' in the foam wall was just that: I needed it tight enough that I could use the door to plug the hole and a bit of a taper to the opening so the door would wedge tight. Of course, I want the finished jamb to be square so it meant I would inevitably have some material to replace. Being that this is a structural component, I filled it with a high density mix of resin, wood flour, and cabosil so that the filler would be of similar density (at least) to the wood.
Styrene based resins do this too, but epoxies generate quite a bit of heat while they're curing. I filled the deep gaps in three separate 'pours' to keep the heat from building up.
Here is the first fill on the biggest gap - you can see the amount of bevel I put on the foam to get a decent seal.
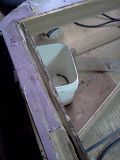
The cedar block in the pic is the uppermost (of three) hard points for securing the door hinges. You can see why I wanted to match or exceed the density of the wood between the jamb and the blocking - a lighter fairing compound wouldn't survive under the compression of a screw as the door is repeatedly opened and closed.
I have a pic of the finished product but, because the glass is clear, it doesn't look all that different from the first pic of it leaning against the wall...
That's it for now, this weekend's project (and into next week) is the next wall panel. This is the last (yay!) panel on the right (curb) side. Because it incorporates the door jamb, it has a couple funny angles on it: nothing that's impossible to glass by any means but it makes it fun to glass.
I got the panel blocked up on the table and fastened down so I can take out the temporary gussets for glassing and not have to worry about the angles changing on me. I also sanded them and got spray foam into the inside corners so I can get in there tomorrow with a drum sander on the drill and give them a rounded fillet. Then I'll skim it with putty and the glass will go on.
Here's a teaser of the panel on the bench. I'm looking forward to glassing it: flat square panels are just boring !
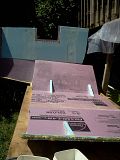
And here's the gaping hole it came from
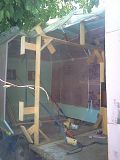
Since the roof is glassed from the back up to where this panel starts, it made sense to incorporate the roof into this panel. I'll do the same with its mates on the other side. You can see on each side of the roof vent (square half-opening on the top) I've staggered the seam so they don't line up. I don't know that it'll make a huge difference but it certainly isn't going to hurt...even if it
is asymmetrical
๐I'll post up as the panel progresses. In the meantime, know anyone who needs a complete set of RV appliances (all working) ?
Just kidding, I'm saving them for the next build......